Pohjoista tehokkuutta
28.11.2013
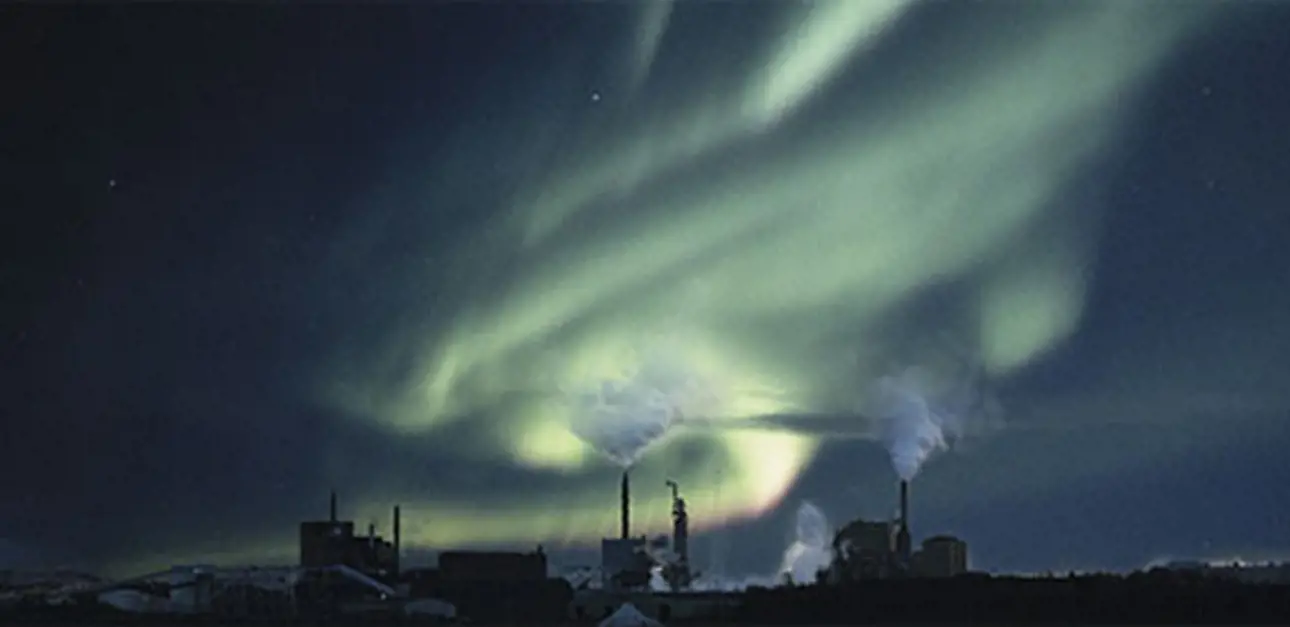
Kemissä sijaitsevan Stora Enson Veitsiluodon tehtaan PK 5:n päivittäinen tuotantokapasiteetti on yli 700 tonnia korkealaatuista LWC-paperia. Vuonna 2011 yhtiö teki päätöksen investoida linjan ajettavuuden ja tuotantotehokkuuden parantamiseen. Valmetin (31.12.2013 saakka Metso Paper) avulla PK 5 päivitettiin tehokkaammaksi; tuotantokatkojen ja hylyn määrää on onnistuttu pudottamaan merkittävästi.
”Halusimme parantaa paperikoneen aika-hyöty-suhdetta eli vähentää tuotantokatkojen määrää ja lyhentää katkoaikaa. Tavoitteena oli myös saada rullaimella syntyvää hylkymäärää pienemmäksi. Samaan aikaan meillä oli käynnissä oma tehostamisprojekti: LWC-paperikoneelle haettiin uutta toimintamallia, jonka avulla tuotantoa voidaan operoida pienemmällä miehityksellä”, kertoo painopaperitehtaan tuotantopäällikkö Markku Åman.
Alusta alkaen oli selvää, että tavoitteita ei saavuteta parilla ihmelääkkeellä, vaan teknologisia parannuksia pitää toteuttaa läpi tuotantolinjan. Huhtikuussa 2012 uudistusten toteuttajaksi valittiin Valmet.
”Voin rehellisesti sanoa, että olemme onnistuneet projektille asetetuissa päätavoitteissa", sanoo painopaperitehtaan tuotantopäällikkö Markku Åman.
Koneen päänvienti uudistettiin koko matkalta
Merkittävin projektissa tehty muutos koski paperiradan päänvientiä, jossa koneen puristinosalle tuli kaksi päällevientilaitetta. Uudistuksilla helpotettiin työtä puristinosalla.
”Mittakaava oli sikäli poikkeuksellinen, että kyseessä oli kokonainen päänvientiprojekti puristinosalta rullaimelle saakka. Heti, kun nauhaa lähdetään viemään, vastaan tulee ensimmäinen uusittu komponentti, PressForce. Nyt linjalla ovat käytössä lähes kaikki päänvientilaitteet, joita Valmetilla on paperilaaduille tarjota. Yleensä uudistukset koskettavat pienempiä osa-alueita”, kertoo Valmetin globaali teknologiapäällikkö Pekka Matilainen.
Myös kuivausosan ajettavuuspaketti uusittiin projektin aikana. Sen alkupäässä sijaitsevat ajettavuuslaatikot päivitettiin vastaamaan tämän päivän tekniikkaa.
”Ennen uudistusta tyypillinen ongelmamme oli, että jossain ilmeni pikkuvika, joka katkaisi prosessin kuivatusvaiheeseen. Tilannetta lähdettiin parantamaan uusilla Vac-teloilla ja ajettavuuslaatikoilla, jotta paperiradan katkoja saataisiin vähennettyä. Ratkaisu osoittautui toimivaksi. Tiettyjä muutoksia tehtiin myös reunojen lepatusongelman korjaamiseksi kaksiviira-alueella (TwinRun), ja niissäkin pääsimme tavoitteisiin”, Markku Åman toteaa.
Muutostöiden yhteydessä päätettiin uudistaa myös kolmospuristimen kaavarointi, koska huono kaavarointi on yksi saostumakatkojen aiheuttaja. Åmanin mukaan uusi kaksoiskaavin onkin toiminut mallikkaasti.
Hylyn määrä kuriin
Projektin aikana tehtiin monia erilaisia teknologiaparannuksia, mutta mikä yksittäinen tekninen uudistus oli merkittävin?
”Rullaimen alueen päänvienti mietitytti etukäteen eniten. Valittu tekniikka alkoi kuitenkin toimia heti ensimmäisestä päälle viennistä alkaen ja on toiminut sen jälkeenkin luotettavasti”, arvioi Åman.
Projektissa käytettiin läpi linjan varsin koeteltua teknologiaa. Pekka Matilainen arvioi, että epätyypillisin PK 5:lle tuotu ratkaisu on rullain-kalanteri -alueella toteutettu keskeltä vienti ja molempiin suuntiin levitys: ”Sen avulla lähdettiin pienentämään käyttökatkossa syntyvän hylyn määrää. Kun vienti tapahtuu keskeltä, rullan pohjamuodostus on heti muutaman kierroksen jälkeen hyvä, eikä hylkyä juuri synny.”
Åman vahvistaa havainnon: ”Aiemmin, kun vienti tuli reunasta, käyttökatkon aikana syntyi hylkyä noin 3 kilometriä konerullaa kohti. Nyt sama lukema on 500–600 metriä. Rullakohtaista hylkyä syntyy siis lähes 2,5 kilometriä vähemmän per katko.” Hylkyä syntyy vähemmän myös siksi, että katkojen määrä on vähentynyt.
Päänvientien takuukokeissa oli määritelty tarkat koearvot päänviennin läpiajoille, ja ne myös saavutettiin. Åman kertoo, että arvoja seurataan jatkuvasti. Suorituskyky ja tehokkuus ovat pysyneet tavoitearvojen mukaisina.
Paperista paperiin kahdeksassa päivässä
”Seisokin aikainen paperista paperiin -toteutus vei kahdeksan päivää. Asennuksissa oli mukana hyvä, kokenut porukka sekä meiltä että Valmetilta. Siinä vaiheessa alkoi varmistua, että teimme oikean teknologiavalinnan.”
Projektin liiketoiminnallinen hyöty ja takaisinmaksuaika perustuvat hyötysuhteen paranemiseen. Kun linja pyörii, sieltä saadaan myyntikelpoista LWC:tä ulos mahdollisimman tehokkaasti.
”Voin rehellisesti sanoa, että olemme onnistuneet projektille asetetuissa päätavoitteissa. Tehokkuustavoitteissa oli mukana myös henkilöstövaikutus. Nyt pystymme ajamaan konetta kahden ammattilaisen voimin. Toki tämä vaatii heiltä monipuolista osaamista, mutta samalla se tuo heidän työhönsä lisää mielekkyyttä ja vaihtelua”, Åman arvioi. Tuotantolinjan kuivassa päässä on kolmas työntekijä.
”Uudistusten ansiosta saamme nyt radan noin 4 senttiä leveämpänä ulos koneesta. Se on pitkälti Vac-telojen ja uusien ajettavuuslaatikoiden ansiota. Jos voisimme leikata myös leikkurilla yhtä leveää rataa, saisimme materiaalihyödyn asiakkaalle asti. Se vaatisi jonkin verran lisäinvestointeja päällystyskoneelle. Esitys aiheesta on vetämässä”, Markku Åman toteaa.