Lumpbreaker felting equipment results in “grand slam” for mill performance
Feb 20, 2025
A pulp mill in the Southeastern United States set out to revamp its pulp drying line to enhance performance and runnability while also exploring ways to increase tonnage on Pulp Dryer #3.
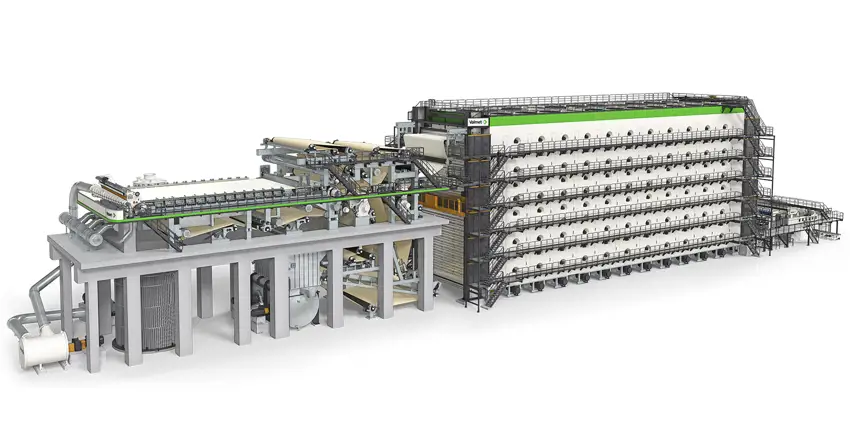
Solution
To address operational challenges, a targeted solution emphasizing both technological enhancements and operational efficiency was created. The cornerstone was the integration of advanced Lumpbreaker Felting equipment which was selected for its capacity to elevate pulp quality and streamline production. Additionally, seven strategically positioned dryer cans were introduced to refine the drying processes, ensuring consistent heat distribution and improved throughput.
Coordinating the installation with the annual shutdown ensured minimal disruption and facilitated rigorous testing. Furthermore, a tailored training initiative was implemented, equipping the operational team with essential skills for adeptly managing and optimizing the upgraded system. This comprehensive approach seamlessly combined technological innovation with workforce knowledge, to bolster performance, efficiency, and overall productivity.
The project was a definite success, and the results were actually better than anticipated! In fact, I’d say it was a “Grand Slam Home Run!” The upgrades to the Lumpbreaker Felting contributed to significant increases in production, as well as improved runnability” - Mill Production Manager, Pulp mill in the Southeast United States
Summary
Location | Pulp mill in the Southeast United States |
Challenges |
To revamp the pulp drying line at a mill to improve performance and runnability. Additionally, the mill sought to explore opportunities to increase the tonnage on pulp dryer #3. |
Solution |
|
Results |
The project concluded on time with the scope of work aligning with the mills annual shutdown. The careful planning and execution yielded impressive results with customer feedback that was overwhelmingly positive. Machine production saw an increase of up to 7-8% after the new equipment was installed with the Lumpbreaker Felting equipment emerging as a key factor in the machine performance. Specific benefits included reduced lumpbreaker picking, superior sheet handling, and overall operational efficiency improvement including significantly enhanced machine runnability. The overall result was improved sheet handling capabilities, increased drying efficiency, and an avoidance of downtime during installation. |
Keywords | Performance, runnability, sheet handling, pulp mill, Lumpbreaker felting equipment, pulp quality |
Discover the Valmet Advantage
With over 225 years of industrial history, Valmet is the OEM partner you can trust. From unmatched process knowledge to comprehensive on-site services and training, we're here to support your success. Explore our resources and download the OEM guidebook today!