DCS Migration and Retrofit
Safe upgrade path for your existing control system

An aging Distributed Control System (DCS) poses significant risks, including unplanned downtime, difficulties in obtaining spare parts, and a shortage of skilled personnel to manage outdated systems. Migrating the existing system to a modern automation platform might be challenging. To mitigate this challenge, Valmet has developed solutions to retrofit existing systems, ensuring a smooth and safe transition to Valmet’s modern DCS.
Proven Expertise
Valmet has successfully replaced hundreds of legacy systems, preserving the familiar workflows while adding the latest capabilities of modern automation systems
Risk-Free Transition
Our step-by-step process is designed for efficient system migrations, minimizing risks and ensuring operational continuity based on the industry-leading process knowledge
Future-Proof Platform
Valmet DNAe provides a foundation for using advanced automation technologies, ensuring long-term value for the next decades of your plant
Functions-preserving upgrade for production continuity
In most DCS migration projects, maintaining production continuity and retaining existing functionalities are top priorities. To facilitate easy operator onboarding, Valmet’s migration paths allow operators to continue using the same base functions as with the old system. Meanwhile, the user interface is upgraded to the latest web-based technology, enhancing situational awareness and extending collaboration with teams outside the control room.
To minimize migration risks and avoid operational disruptions, the existing control logic, parameter values, and alarm settings are retained when restarting the plant with the new system. Faster deployment and testing reduce process downtime during system replacement. This functions-preserving approach provides a safe foundation for automation system modernization without compromising plant operations.
The migration begins with a thorough evaluation of the existing DCS to ensure that no critical components or configurations are overlooked. This way, we ensure that the system provided to your plant will be tailored according to the specific needs of the plant. Experts conduct a thorough examination of the existing system at your plant and provide the best possible solution to your future needs.
Key Activities
Data Extraction: Collect detailed information from the legacy system, including:
- Control logic and process parameters.
- Database of existing applications
- Alarm settings, interlocks, and other parameters
- Operator interface layouts and workflows
System Mapping of how to translate existing functionality into a migration plan, ensuring all processes and controls are notified. Identifying potential challenges and planning mitigation strategies to guarantee a smooth transition between the legacy system and Valmet's new DCS.
Functional description creation and System design cover developing new programming descriptions and application loops that accurately match the legacy system’s functionality. Our global network of automation professionals provides specialized know-how about different systems and processes. Our advanced tools are available to support the replication of functions of your legacy system to Valmet's DCS.
The system design preserves existing functionality and ensures operators can continue working as before, without extensive retraining, and quickly understanding the new system.
Key activities
- Based on functional descriptions, collaborative control meetings with the customer’s team can be held to review functional descriptions and refine process controls as needed.
- HMI Sketching as operator screens are designed to reflect the familiar look and feel of the old system, with optional usability enhancements if desired.
- I/O Mapping tailored to your legacy system to ensure seamless integration with existing field devices.
Extensive testing ensures that the new system performs as expected before deployment. Risks are minimized during commissioning.
Key Activities
Factory Acceptance Testing (FAT): Simulate the migrated system in a controlled environment to validate
- Control loop accuracy and process response.
- Alarm handling and interlock functionality.
- Operator interface usability.
The functional descriptions are being used as the basis for successful FAT.
Valmet’s commissioning strategy ensures minimal disruption during the transition to the new system.
Efficient planning of key actions:
- Performing system replacement during scheduled plant shutdowns, avoiding unplanned downtime.
- Optimizing the work done during the shutdown and planning tasks carefully so that the work that can be done outside the shutdown will be done beforehand or afterward. Efficient work during the shutdown period will minimize the needed time for shutdown.
On-Site Validation: Conduct loop checks, communication tests, and final system validation before startup.
Competitiveness guaranteed
While functionality-preserving replacement focuses on operational continuity, the modular system adapts to evolving operational needs. Long-term improvements are always available throughout your plant's lifecycle and include:
- Combining multiple different automation systems in one single system
- Process Optimization: Tailor controls and functions to improve efficiency and reduce variability
- Enhanced UX Design to modernize operator interfaces for improved usability and decision-making
- Advanced process controls and Mill-Wide Optimization tools
- Data management and Advanced Analytics for predictive maintenance, energy management, and process diagnostics
- Lifetime system compatibility guarantees that there's always an upgrade path available
- ISASecure System Security Assurance Cybersecurity Certification according to ISA/IEC 62443-3-3 (SSA) and ISA/IEC 62443-4-1 (SDLA) standards
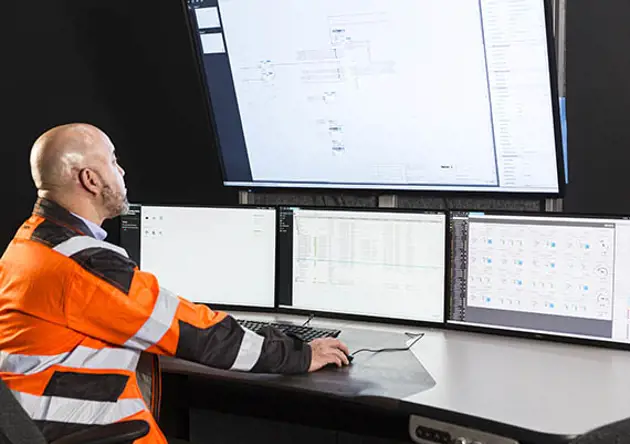
Our Distributed Control Systems