Valmet wastewater solutions save energy and chemicals
Apr 9, 2016
Tampere Water recently installed several Valmet total solids measurement devices and a sludge dewatering control package at its Viinikanlahti wastewater treatment plant in Tampere, Finland.
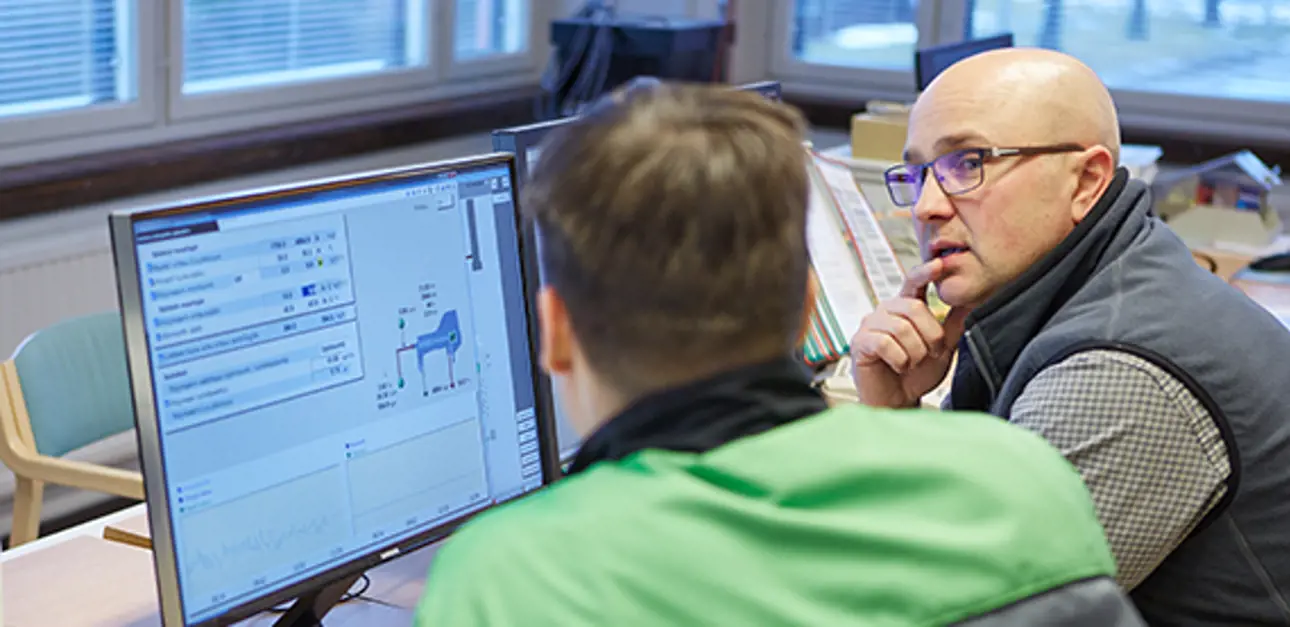
After the start-up at Viinikanlahti, immediate results were visible, from savings in pumping energy to improved anaerobic digestion and subsequent sludge dewatering. In addition to improved solids control, the measurements now also provide a valuable insight to plant operation, with real-time solids information replacing infrequent laboratory analysis. Maintenance Engineer Ari Oksanen comments: “We can now see process parameters in kilos rather than cubic meters, which is a great help in optimizing the different stages of treatment.”
The biological and chemical wastewater treatment in Viinikanlahti is based on an activated sludge process coupled with phosphorus precipitation by ferric sulfate. The process consists of screening, grit removal, primary sedimentation, aeration and secondary sedimentation. Wastewater sludge is digested in anaerobic digesters after which the sludge is dewatered by centrifuge. Biogas from the digester is used to generate electrical energy and heating for the plant.
Although the highly efficient treatment methods meet the requirements of Finnish and European Union legislation, Tampere Water decided in 2015 to enlist Valmet’s help to improve its chemical and energy efficiency. Heikki Syrjälä, Technical Manager at Tampere Water, valued Valmet’s input to the project, “As we are planning a new treatment plant, this was a good opportunity to discover what the latest technology has to offer. The quality and workmanship displayed by Valmet has been excellent,” he says.
Total solids measurement
|
Three Valmet Total Solids Transmitters (Valmet TS) are in use to measure total solids after the primary clarifiers, before the digester and before the dewatering centrifuge. The four circular primary clarifiers in Viinikanlahti allow solids in the wastewater to settle to the bottom of the clarifier before being pumped to the sludge thickening tank. Prior to the Valmet TS installation, pumping from the four clarifiers was controlled in a timed sequence, which meant that from time to time a clarifier would be emptied of solids and only water would be pumped to the thickening tank. With Valmet TS measuring the total solids content, the pumping sequence from the four clarifiers is now controlled to a minimum solids content, avoiding excess water being pumped to sludge thickening. According to Sami Ilomäki, Operating Engineer, the reduction in pumping has been quite dramatic: “We used to pump 76 m3 an hour to thickening. Now, with accurate total solids control, that’s fallen to only 50 m3 an hour, saving pumping energy and reducing excess water to thickening.” With a second Valmet TS transmitter after thickening, the measured solids content to the digester has now increased from 3.5% to 5%. “The higher solids content in the digester reduces the heating demand and has also resulted in less foam,” says Ilomäki. As well as needing less heat, the optimized solids content also increases digester residence time, producing more biogas.
![]() |
Viinikanlahti engineers Sami Ilomäki and Ari Oksanen are very happy with the operation of the Valmet TS. |
Centrifuge control
After anaerobic digestion, the sludge is dewatered before being transported by truck for use in agriculture, landscaping and other soil improvement uses. Sludge dewatering is carried out in the centrifuge, where water is forced from the sludge. The dried sludge (dry cake) is then taken by conveyor to be trucked away from the plant. The liquid centrate from the centrifuge is recycled back into the process. As Syrjälä explains, “Sludge dewatering is a complicated process using both energy and chemicals. To avoid wasting either of them and save on transportation costs, optimization is necessary. Running the process manually in the optimal way is difficult.”
![]() |
![]() |
|
The resulting dry cake which is taken from the plant by truck. | Valmet DS measures the solid content of the dry cake as it falls to the conveyor. |
Valmet optimization of sludge dewatering
![]() |
|
Janne Katiska, Valmet engineer and Sami Ilomäki at the Valmet SDO operator interface in the treatment plant control room. |
The Valmet solution is dewatering optimization with the Valmet SDO (Sludge Dewatering Optimizer) control package. Valmet SDO is a small-scale Valmet DNA control system employing multi-variable model predictive control (MPC) to control the centrifuge operation. A Valmet TS transmitter is used to stabilize the mass flow to the centrifuge, now measured in kilos of sludge per hour. In the first phase of optimization, performed in December 2015, this allowed dewatering polymer to be controlled as a ratio to the mass flow rather than the cubic meter-based flow rate previously used. With the mass flow under control, the second phase of optimization in January 2016 was to optimize solids in the centrate and moisture in the dry cake with a combination of torque control and polymer.
![]() |
According to Sami Ilomäki, “With help of the Valmet LS measurement it has been possible to reduce the amount of recirculating material by 50%.“ |
A Valmet Low Solids Measurement (Valmet LS), is installed in the centrate outflow and another specialized measurement, Valmet DS, measures the solid content of the dry cake as it falls to the conveyor. This is where the multivariable model predictive control, unique to Valmet SDO, comes into play. As the centrifuge torque is increased, more water is extracted from the sludge and the solid content increases in the dried sludge, but at the same time centrate solids increase to be wastefully re-circulated through the plant. Increasing polymer dosage increases the solid content of the dried sludge and also reduces centrate solids, so the control combines the optimum torque and correct polymer dosage to save both energy and chemicals while achieving the optimum amount of reject solids and a higher dryness in the dry cake from the centrifuge.
More good results
The new measurements and centrifuge dewatering control have been very successful, Sami Ilomäki reports: “Previously, our centrifuge operating parameters had to be very much on the safe side to limit the recirculation of reject (centrate) solids. We have now been able to reduce reject solids by 50%.” Ilomäki sees room for even further improvement as people become more familiar with the controls: “The controls are easy to operate and the system is very user friendly, allowing us to easily adjust parameters and even measure the effectiveness of different polymers. We now have a much better picture of what is going on in the treatment process.”
For more information:
Heli Karaila
heli.karaila@valmet.com
Tel. +358 40 543 4724
![]() |
Good correlations to laboratory results were obtained immediately in the first two months after startup. Top to bottom, dry solids to digester, centrifuge centrate and dry cake solids. |
Related articles