Valmet’s technology helps to reduce CO2 emissions in UK
Sep 30, 2014
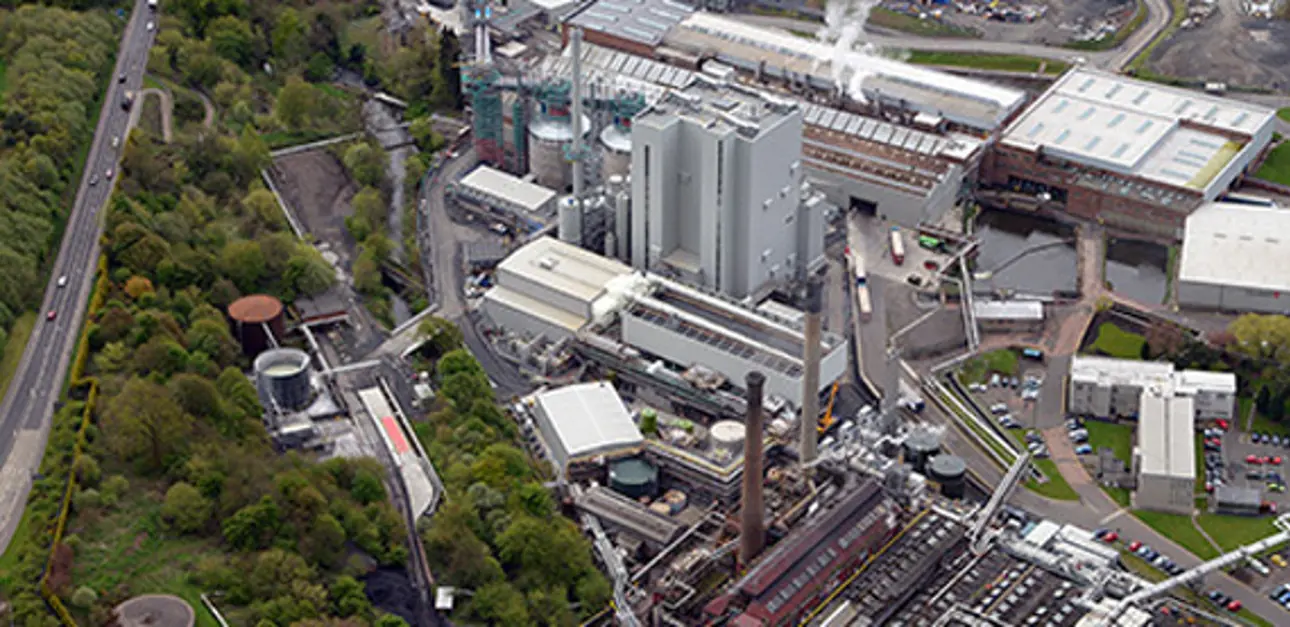
Valmet handed over a new biomass boiler plant and flue gas treatment for RWE Innogy UK’s Markinch combined heat and power plant (CHP) in July 2014 following a commissioning period and test-runs. The plant is located in Fife, Scotland, and is the largest of its type in the UK. The new plant provides the Tullis Russell Papermakers with steam and electricity to run the facilities. In addition, excess electricity is exported to the grid.
The new plant helps Tullis Russell reduce its fossil fuel emissions and significantly contributes to Scotland’s ambitious renewable energy targets. Replacing the paper mill’s 60-year-old coal-fired plant with this new biomass-fired plant reduces CO2 emissions by 250,000 tonnes per annum. Also the amount of waste wood currently ending up at the landfill and there, over time, emitting methane is reduced since the main fuel for Valmet CFB Boiler (formerly CYMIC) is recovered waste wood.
The new biomass boiler provides the Tullis Russell paper mill with a more sustainable, efficient and reliable supply of steam and electricity.
Robert Dunk RWE’s project engineering manager said: “RWE is delighted to take the Valmet CFB Boiler into operation as part of the largest portfolio of renewable energy technologies in the UK. The biomass boiler will help provide steam and electricity to the adjacent Tullis Russell paper mill and export electricity to the Grid whilst significantly reducing CO2 emissions. The successful handover is the culmination of close cooperation and partnership between RWE and Valmet since 2010 and is testament to the dedication of the Valmet team.”
The new state-of-the-art facility will be cleaner than the coal fired plant it replaced. Improvements made to the steam supply system will also reduce the likelihood of noise from steam releases.
The CHP plant’s installed capacity is 50 MWe. It has the capability to supply up to 120 tonnes of industrial steam per hour for paper manufacturing. Out of the produced electricity the paper mill will consume approximately 14MW and approximately 25MW will be delivered to the national grid.
The plant has been in commercial operation since February 2014 with full handover of plant in late 2014.
An area equalent to the size of four football pitches
This was Valmet’s fourth boiler project in Scotland during the past 15 years, portraying Valmet as a trusted partner among many customers in the UK. A successful project like this provides a good reference and can serve as a springboard for further business in the UK and beyond.
“This project was pretty massive both from the size and timescales involved. To put it into perspective, the CHP plant fills an area equivalent to the size of four football pitches and more than 1 million man hours have been invested in its construction. At the height of the construction process, there were around 650 people employed at the whole site with around half of them working at our boiler site,” describes Valmet’s Project Manager Peter Anson.
Enabling and construction works at the site started in 2010, prior to Valmet’s arrival in July 2011. The new boiler was being built within the grounds of the existing paper mill. Some buildings dating back to 1809 had to be demolished and new foundations laid to make room for the new power plant. This was not a simple exercise as the ground underneath was scattered with unmapped, disused mine shafts.
“This project was a showcase of a multinational site. In total, we had people from 11 different countries working together. We had to comply with the strict safety regulations of the UK. In addition, health and safety was of paramount importance to our customer and this was an area which we gave particular focus, working closely with colleagues from RWE. Our construction activities were subject to intense scrutiny at times and, at the project’s height, we had 5 dedicated HSE professionals at the site. Furthermore, local media, politicians and unions showed great interest since this was a dedicated category 1 site under the NAECI agreement. We worked in close cooperation with all these stakeholders. For example, monthly meetings were held with the local labour unions, which ensured smooth industrial relations,” Peter continues.
Technology informationA combined heat and power (CHP) plant produces both electricity and heat which makes it a highly energy efficient technology. Even up to 20% savings in energy can be reached compared to the separate production of heat and electricity. This leads to lower fuel consumption, fuel costs and carbon emissions. Valmet CFB Boiler, supplied to the Markinch CHP plant, utilizes proven circulating fluidized bed (CFB) technology. The boiler’s capacity is 155 MWth and it is fuelled by approximately 90% recovered waste wood and approximately 10% virgin wood, sourced from sustainably managed forests. The biomass requirement is around 400,000 tonnes per annum. The new technology novelty in this boiler makes it possible to reduce the required shutdown time. The main advantage of Valmet CFB Boiler is its superb fuel flexibility. Most of the over 70 references around the world are multifuel boilers, which combust different types of biomass and fossil fuels in continuously varying proportions. Co-combustion is an environmentally benign method of combining excellent reliability and availability with a great potential to optimize operational costs by allowing several fuel alternatives. The stack at the Markinch biomass CHP provided a new landmark in the area with a height of 75 meters. Upstream of the stack, Valmet also delivered a flue gas treatment plant based on bag house filter technology. The process is equipped with activated carbon and hydrated lime dosing which, together with the filters, ensures that the stringent emission limits demanded by EU directives and the Scottish Environmental Protection Authorities (SEPA) are fulfilled. To ensure compliance, the emissions are monitored by a continuous monitoring emission system (CEMS). |
The NAECI agreement
The National Agreement for the Engineering Construction Industry (NAECI) sets comprehensive terms and conditions of employment for hourly-paid engineering construction workers on major engineering construction projects, repair and maintenance sites and events/outages throughout the UK. Read more.