AkzoNobel and Valmet, two specialists working together
Jan 15, 2018
The history of salt production in the Netherlands started in the early 1900s with Royal Dutch Salt Industries (KNZ). Today, its successor AkzoNobel is the leading producer of salt. One of the company’s production sites in the Netherlands is located in Delfzijl, where production runs with Valmet’s automation, Valmet DNA.
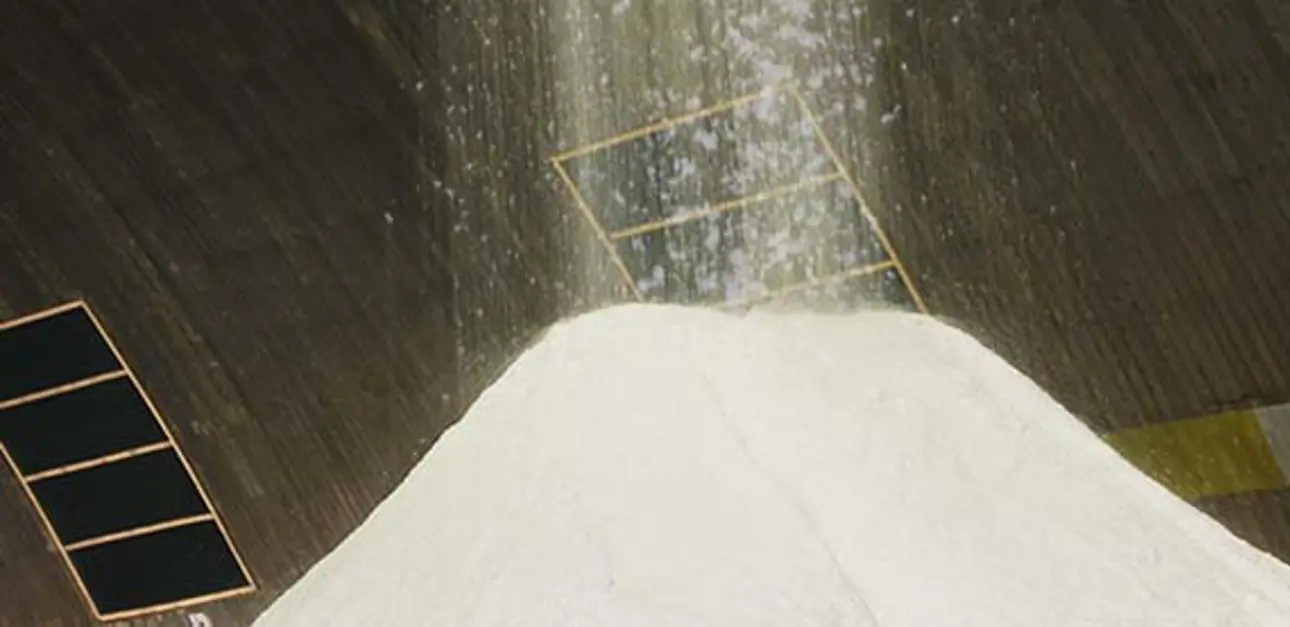
AkzoNobel, a multinational company with operations in more than 80 countries, is a leading producer of paints, performance coatings and special chemicals for consumers and industry. Salt is produced at three sites. The Chemical Park in Delfzijl was once entirely owned by AkzoNobel. Now, the area is considered as a chemical cluster, creating a unique group of companies working together within the chemical industry.
Eneco Bio Golden Raand, one company near the cluster, is an importan supplier of energy and steam for AkzoNobel. In fact, a lot of steam is needed to produce salt. The biosteam from Eneco makes the salt production even more sustainable.
The salt is sold mainly to the chemical industry. The so-called “city salt” is also used on the roads for de-icing. Johan Huizenga, Maintenance Engineer (in picture), explains how AkzoNobel differs from competitors: “We are a reliable supplier with a good reputation who delivers high volumes efficiently.”
Salt business with extensive automation
The brine drilling fields are located about 20-30 kilometers from Delfzijl, in Heiligerlee and Zuidwending. There, water is injected into the ground to a depth of roughly 1,000–1,500 meters where the mineral salt at those depths turns into brine.
Pumping stations transfer the brine through pipelines into a basin near the salt factory. After being stored in the basin, purification and the drying process take place. At the end of this process, the salt is stored until it is delivered to customers.
Since the 1980s, AkzoNobel has trusted Valmet’s automation. It first started with Damatic and now continues with Valmet DNA. Today, the entire extensive process is taken care of using Valmet’s automation. From AkzoNobel, Johan Huizenga and Rein Kruger, Automation Engineer, are both very familiar with the system. Johan Huizenga explains: “At the time when the digital Damatic system was selected, Valmet’s automation was the first to have sequences in addition to controls and interlockings. Simply, it was more sophisticated than the others available on the market.” Already in the 1980s, AkzoNobel was a forerunner in using advanced technology to stabilize its production.
Stable process through automation
To keep the process stable, several advanced Valmet DNA features are in use daily. For instance, with Valmet DNA Historian, the customer is able to process a large amount of real-time process data, such as measurements, set points and alarms, which can be stored in the history databases. The collection cycles are typically 1 s or 10 s.
Rein Kruger (in picture) explains: “We have plenty of data available. With its help, for instance, disturbances can be analyzed, and we are able to learn about the failures. We can also easily track operators. The data is used effectively and widely in our organization, together with our own office database.”
Johan Huizenga continues: “The importance of automation to the stability of the process is notable. It makes our work much more efficient. Sometimes, with certain process enhancements, we can even see improvements to the end product.”
User interface
In the factory, two control rooms for salt production are available. Two unmanned control rooms and a smaller back-up station are located in the brine fields. The fields can be accessed remotely from the main control room. Normally one operator works in the control room and four in the factory for a total of five operators during each shift.
Paul Janssen, Process Operator, (below, in the control room) confirms that Valmet DNA provides him with a lot of easily accessible information. The interface is called Valmet DNA Operate, which features user-friendly design and operation. Paul Janssen has had a long career with AkzoNobel; he once even used the first Damatic system. As not everyone has such a long history in the company, new operators get extensive hands-on training.
“Visibility of the events in the process is important as well as the historical data available within one system. In the windows on the screen, every operator can have their own favorite arrangement of all the information on the displays,” explains Johan Huizenga.
Roadmapping – planning for the future
Technological roadmapping, which is prepared jointly by AkzoNobel and Valmet, is a long-term planning tool. Potential critical issues are listed, such as products or product support that are being phased out, or adding technological innovations that better support the customer’s process. All factors are analyzed and the required changes outlined in optimal order and time. Using this information, preventive maintenance can be done effectively as part of the service contract.
With changes and upgrades, timing is important. Rein Kruger states: “We know in advance which factory will be shut down for a certain number of days. Then, we make a detailed plan with Valmet on how and when to proceed with the changes. Completion of a project might take about two weeks. So, we have to plan it for each section. A complete shutdown of the plant will not take place, the process has to run 24 hours a day, 365 days a year.”
Roadmapping helps AkzoNobel to always know the status of its automation system. And thorough planning leads to foreseeable budgeting as well. Johan Huizenga confirms: “We have a complete plan with Valmet from 2016 to 2020/2021. Within that time, for instance, the rest of the CIOs shall be exchanged.”
Testing in Valmet's premises: Jaap-Jan Krikken, Service Supervisor from Valmet and Rein Kruger.
When the automation system is well maintained, the customer gets a better return on investment (ROI). The main target is to have the process operate efficiently and avoid unplanned shutdowns.
System upgrades step by step
Advanced automation features are constantly evolving. “During the years, several technological upgrades have been made in line with our scheduled factory shutdowns. And this is always to our benefit to make the process even more efficient,” states Rein Kruger.
For instance, during 2005 and 2006, the aging automation system was upgraded to the Valmet DNA system. This is an easy way to do upgrades, since not everything has to be replaced at the same time. The upgrade process can be carried out step by step, while always securing the stability of the process. At the same time as the upgrade, several Siemens programmable logic controllers (PLCs) were replaced at the drilling locations and DNA was added to the pump station in Midwolda.
Johan Huizenga lists: “The PCs, servers and ACNs have been upgraded with the latest technology.” The Application & Controller Node (ACN) family of controllers and I/O units build a reliable platform ¬– from basic alarm and monitoring up to the most advanced applications. When moving to ACN controllers, an ACN was first installed on a smaller part, a process station for the pumping station. Now the entire production is covered by the same automation system, from brine fields to centrifuges.
Henk ten Kate, Engineering Manager (above, in the control room with Rein Kruger), is one of the main contacts at Valmet. “First, we upgraded two CIO cabinets with new MIO cabinets. The upgrade enables more powerful and smaller units compared to the earlier units. In close cooperation with AkzoNobel we have delivered tailored cabinets with for example terminal boards to handle cross wiring between field instruments and MIO units for centrifuges.
The latest delivery includes two customized small cabinets with an overvoltage protection feature to be located at the brine fields. At the time of this interview, the two cabinets are at the Valmet location in Bunschoten for the factory acceptance test (FAT). Delivery and installation will follow in the next few weeks.
Good customer service is the cornerstone
How would you evaluate service and support from Valmet? Johan Huizenga replies: “Over the years, a good relationship has been created with Valmet. We are able to reach our contacts easily and problems are solved quickly. Valmet is really close to us. And most important is that they always come to us with a solution.”
Rein Krugeragrees with his colleague. He adds: “Valmet is flexible and very open-minded towards new solutions. The experts are always ready to help us.”
To run a factory successfully from the automation point of view, you need good hardware, sophisticated software and experts to work together with you. With the help of systematic system upgrades and preventive maintenance from Valmet, AkzoNobel is able to run its process reliably.
And as Rein Kruger puts it: “It is our business to run the factory, produce salt and make our earnings. Together with a reliable partner, Valmet.”
For more information:
Henk ten Kate
henk.tenkate at valmet.com