Exceptional board quality achieved on a high-speed board machine featuring automated retention control
Nov 16, 2023
Kipaş PM1 paper machine is located in the epicenter of the earthquake that struck Turkey and Syria in February. Following the earthquake's devastation, the 450,000 ton/year capacity board machine and machine hall in Kahramanmaraş were severely damaged. Thanks to the dedicated efforts of the Kipaş Kağıt and Valmet teams, production resumed in May. The goal for the high-speed machine, running at 1500 m/min, isn’t just to resume operations but to produce paper even more efficiently than before.
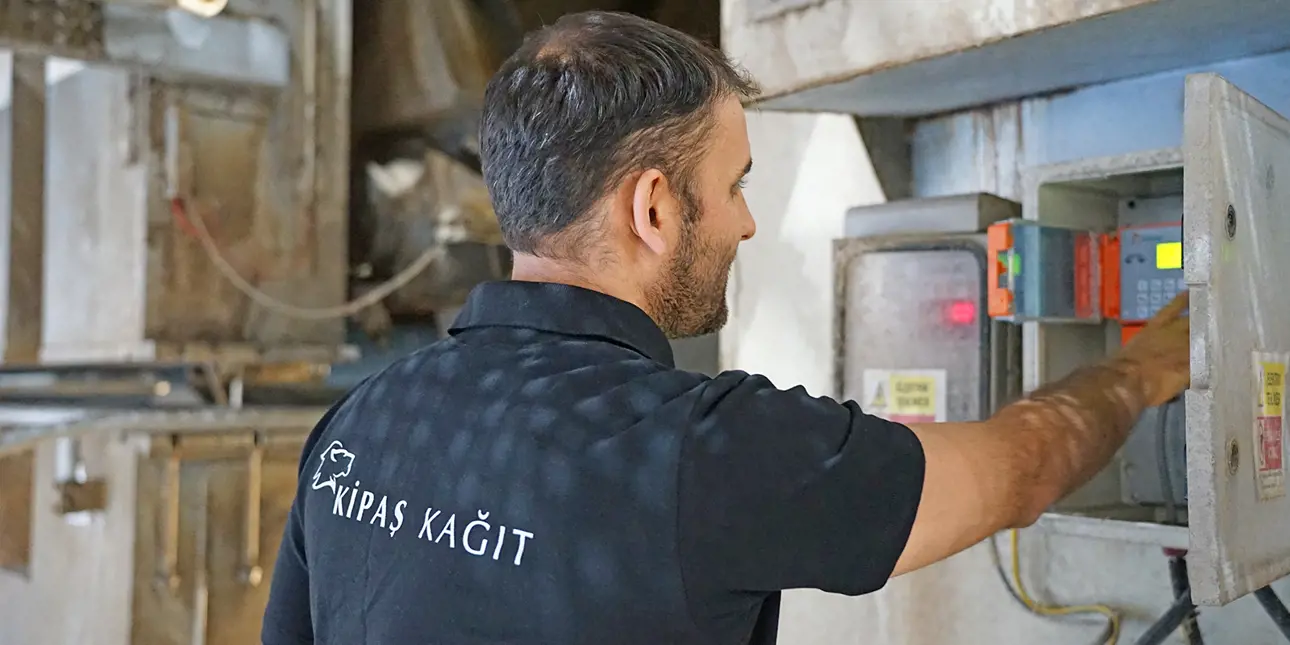
Maintaining competitiveness through continuous real-time monitoring of retention
Kipaş PM1 is equipped with Valmet Retention Measurement (Valmet RM3), the older version of Valmet RM5, which today takes retention measurement one step further with its advanced features. Kipaş PM1 has been using two Valmet RM3 devices since its startup in 2014. Ali Özkan, Production Manager, notes that when they initially invested, RM3 devices were one of the most critical tools for their paper production: "Traceability is crucial in paper manufacturing. The more accurately and healthily you perform this task, the faster and more consistent your production becomes, enhancing quality. In today's economic environment, customers demand higher quality and more affordable products. Therefore, the automation and analysis systems selected at PM1 since its installation increase our competitiveness.”
A stable wet end ensures high-speed board machine production
Muhammed Konak, Electrical Automation Maintenance Manager, emphasizes the importance of stability in the wet end for smooth subsequent processes in high-speed board production: "Today, everything that speeds up the process is essential for production. The Valmet RM3s help us measure and control headbox and white water consistency. The analyzer is reliable and maintains stability in the wet end of our fast-running board machine.” Konak also highlights RM3's precise measurement capabilities: "RM3, unlike other consistency measuring devices, offers highly precise measurements. We have consistency transmitters measuring between 6-12% in pulp preparation. However, the RM3 measures between 0-1%. Other devices may not achieve this level of precision.”

From left to right: Hamit Demir (Valmet Turkey Automation Business Line Sales Manager), Mesut Okuducu (Electrical Automation Maintenance Chief), Muhammed Konak (Electrical Automation Maintenance Manager) Ali Özkan (Production Manager)
Reduced chemical usage and enhanced efficiency
In response to rising chemical prices, Kipaş established its own production facility lately. The company set up a starch factory at the same location as PM1 and relies on RM3 devices for efficient use of wet end chemicals. Ali Özkan explains, "RM3 allows us to use accurate dosage of chemicals. This makes our white water cleaner, reduces the number of paper breaks, and reduces our chemical consumption. With the data provided by this system, we can also control factors such as paper grammage and moisture fluctuations which improve the machine directional (MD) profiles of the board.”
During the earthquake, we truly saw the dedication and support of both Valmet Global and Valmet Turkey.
Valmet's dedication and unwavering support in times of crisis
Ali Özkan reflects on the invaluable support provided by Valmet during and after the earthquake: "During the earthquake, we truly saw the dedication and support of both Valmet Global and Valmet Turkey. After the mill site was safe, Valmet arrived without hesitation with six teams and meticulously went through everything, aligning the machine and assisting remotely in all automation controls. We trust Valmet.”
Hamit Demir, Valmet Turkey Automation Business Line Sales Manager, highlights that Kipaş Kağıt has consistently remained at the forefront of adopting the latest technology. He adds, "Kipaş Kağıt has always been an avid follower of the most recent technological advancements in production. Valmet RM3 is currently being used at PM2 in Söke, while Valmet RM5 will be used at the newly commissioned PM3. PM1 is also planned to switch to RM5 in the coming days."