Engineering top-notch performance
Dec 5, 2024
Emami’s latest investment in their PM 3 line focused on producing high-quality writing and printing paper, achieving remarkable results.
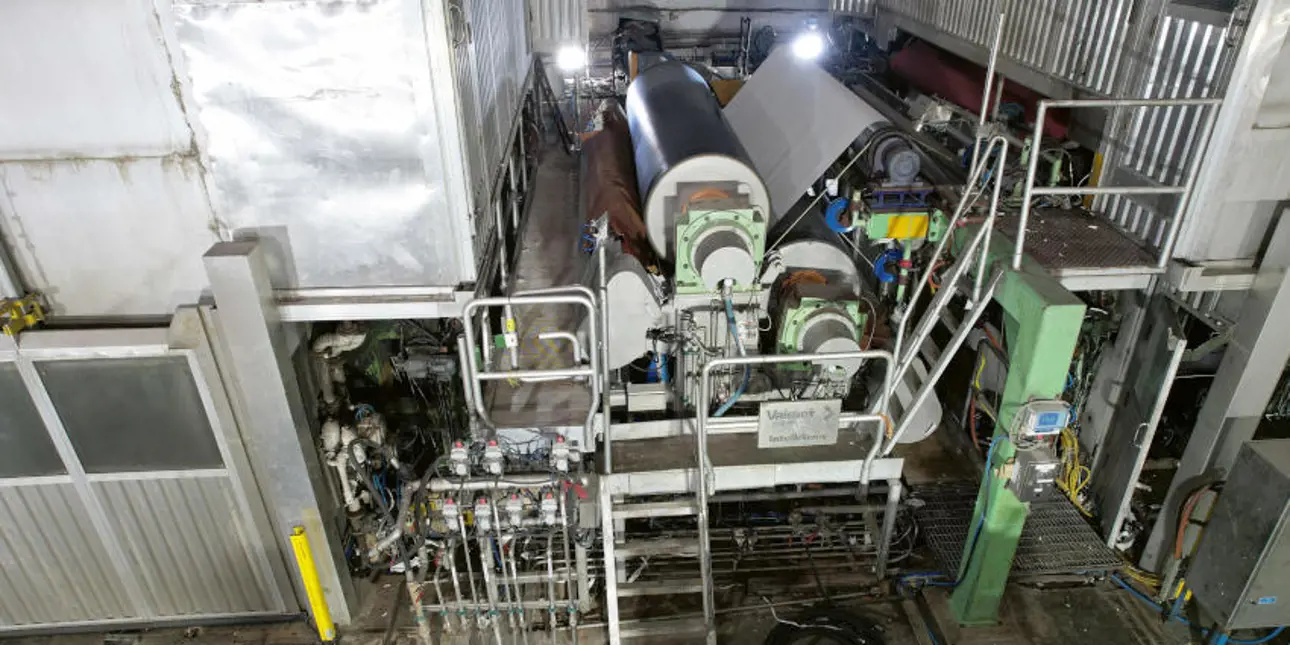
The primary challenge was to remove the existing Hydra-Nip unit and install Valmet’s metering size press in a limited space.
Emami Paper Mills Ltd. has been operating since 1981. This prominent Indian manufacturer, which specializes in newsprint, writing, printing paper, and multilayer coated board, took a significant step toward the diversification of their products with their investment in Valmet’s IntelliSizer size press and a size kitchen for their PM 3 project at the Balasore site. Recognizing the declining newsprint market, Emami aimed to introduce high-quality writing and printing paper to their portfolio. Through a partnership with Valmet, Emami successfully transitioned their focus while maintaining operating excellence.
Valmet worked closely with the Emami team during the PM 3 project.
A world-class solution
The primary challenge was to remove the existing Hydra-Nip unit and install Valmet’s metering size press in a limited space. This upgrade would enable Emami to produce surface-sized writing, printing, kraft, and newsprint grades on demand. “Valmet accepted the challenge and installed the size press with air turn, a single-point scanner, and a tail threading system. Their commitment to quality and safety standards has been commendable,” says Mr. S. Sreejith, General Manager (Mechanical) at Emami.
Reliable solutions and strong local support from Valmet boosted efficiency, productivity, and sustainability.
A proactive and responsive partner
The cooperation between Valmet and Emami was very productive. Throughout the installation phase, the partnership’s success was driven by effective communication and a proactive approach, even with challenges like the rope threading system at the post-dryer section. “Valmet’s team was responsive, ensuring the machine started on time, even under tight schedules and operational constraints,” Mr. S. Sreejith adds.
Emami took a significant step toward the diversification of their products with their investment in Valmet’s IntelliSizer size press and a size kitchen for their PM 3 project.
Exceptional end-product quality
The results have exceeded expectations since the installation. Emami reports that their end-product quality has been exceptional, receiving positive feedback from end users. The production levels and machine efficiency have also aligned perfectly with their targets, allowing them to meet market demands flexibly. Valmet’s IntelliSizer size press and the size kitchen systems have proven reliable, with strong support from Valmet’s team when required. “The starch preparation system, combined with automation, has provided consistent quality, allowing us to maintain precise operational control,” he says.
Valmet’s innovative engineering enabled Emami to diversify production while maintaining top-class quality.
Excellent engineering and performance
Since the installation, the system’s energy efficiency, water consumption, and overall runnability have all met or even exceeded the set targets, strengthening the investment value. Despite limited space and a tight project schedule, the size press and size kitchen systems were delivered on time. “Valmet has not compromised on safety standards, and their detailed engineering was outstanding,” Mr. S. Sreejith says.
Since the installation, the end-product quality has been exceptional, receiving positive feedback from end users.
Looking forward
Emami is very satisfied with the overall performance of the equipment delivered by Valmet and has expressed their intention of continuing the collaboration in future projects. “We’re happy that we’ve selected the right supplier for our PM 3 project. We will recommend buying Valmet products and will be interested in working with the Valmet team in our future projects,” Mr. S. Sreejith says. The success of this concept is a symbol of the importance of innovative technology, strong collaboration, and precise execution in driving forward the paper industry.
“We selected Valmet because they are the leader in technology. In our case, we were constrained by the lack of space at the size press. Most size presses need one more lane, but Valmet’s size press can be accommodated in limited space, so fewer dryers needed to be removed. That was the major attraction. In addition, they are the leader in this, so we thought that Valmet was the right partner for us,” says Mr. Ashish A Gupta, Senior President and Unit Head of Emami.
Text Monika Cieślak, Weeraya Netwong, Akhil VP