Mondi Syktyvkar: Repaired to perform
Dec 21, 2021
When Mondi Syktyvkar needed repair work in its recovery boiler RB7, it turned to Valmet to ensure a job well done and minimized downtime.
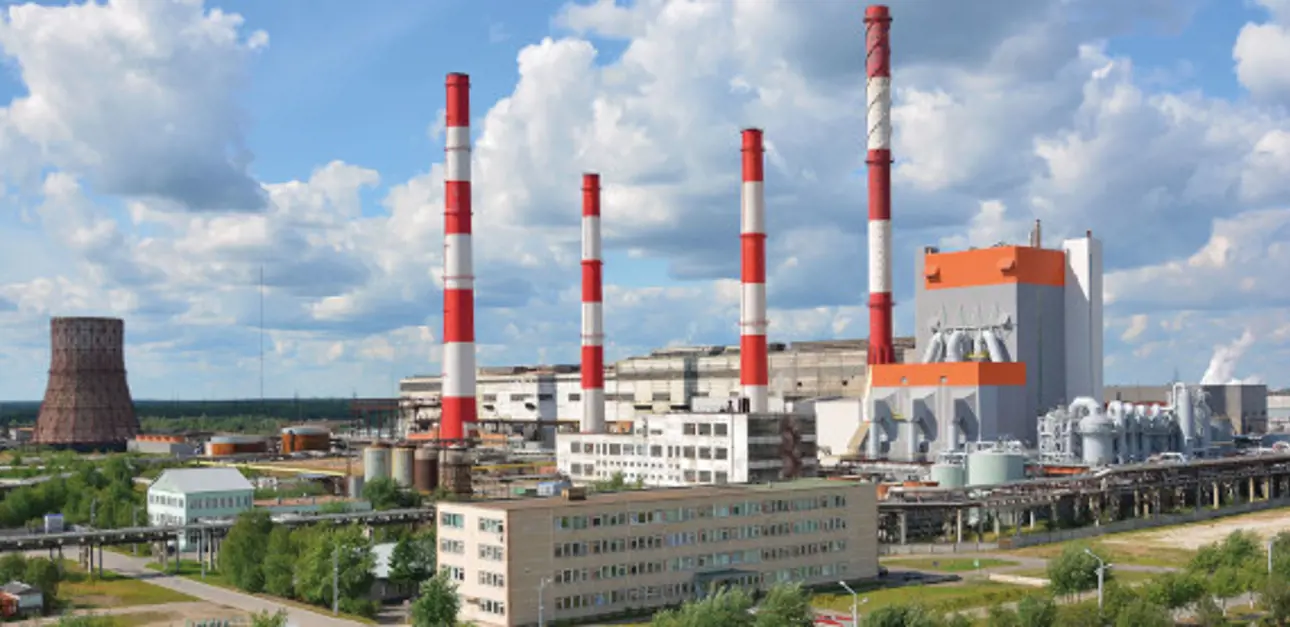
A few years ago, Mondi Syktyvkar, a leading Russian pulp and paper mill and the largest domestic paper producer, faced a problem with the welds in its 3,750-tds recovery boiler RB7, which was started up in 2010. The detected defects in the area of the welds were causing concern. What if the welds failed? Nobody wanted to imagine the effect on the whole process.
The mill contacted Valmet – even though it was not the original boiler supplier. “Valmet has huge experience in repairing this type of boiler. Experience was especially important, since the work had to be performed with composite steels, which are not common in Russia,” says Dmitry Shein, Deputy Head of Recovery and Lime production, Fiber Production, at Mondi Syktyvkar.
Work finished ahead of schedule
In the summer of 2019, Valmet’s boiler service professionals – some 80 people from Sweden, Finland and Russia – traveled to Syktyvkar. Their job was to repair 1,600 welds on three different levels of RB7. Valmet provided the tools and manpower with Russian safety cards and welder certificates.
The target was to work for 19 hours on each tube, and the whole project would take five weeks.
“From the first day, it was clear that Valmet worked as a single strong and cohesive team with a clear hierarchy and knowledge of the business. The pace set by the team was decisive for achieving the goal and allowed us to perform all the work according to schedule, taking the additional work into account,” Shein adds. “The Valmet team always focused on us. All our recommendations or suggestions leading to shorter equipment downtime or an improvement in the quality of work were accepted objectively and agreed in the shortest possible time.”
Thanks to detailed planning, hard work and fruitful cooperation with the customer, each tube took only 11.6 hours to repair.
Back to the site in 2021
More repairs were planned in 2020, but the Covid-19 pandemic put them on hold. In 2021, the Valmet team was invited back to the site, and the work continued in a ten-day shutdown.
This time the project scope was smaller – initially, only 748 welds – but the welds were located in more complicated boiler sections. At the customer’s request, an additional 134 welds were worked on.
According to Nikolay Shulikov, Project Manager, Valmet, the panels were much larger – up to 5.5 meters high and 1.5 meters wide. “This all required even more planning than earlier, as well as high accuracy in cutting the tubes and reinserting them in the existing panels,” he says.
The project was a success this time too. “The Valmet team once again carried out the work professionally and on time. Unexpectedly, they also had to work on defects that were discovered during a boiler inspection, preventing the boiler start-up and requiring immediate elimination,” adds Shein. “Valmet understands how much the downtime of the plant’s main equipment – the recovery boiler – costs and does its utmost to reduce repair worktime.”
The results exceeded the mill’s expectations, leading to additional work on the aerodynamic ledge. Shein continues: “We expect the same team of professionals and like-minded people to complete the work on replacing welds in RB7 in 2022.”
Text : Marjaana Lehtinen
Photos: Mondi Group