Valmet’s maintenance-related Industrial Internet solutions improve heating plant availability
By tracking the condition of its Hervanta heating plant with Valmet’s Industrial Internet (VII) applications, Tampereen Sähkölaitos recognizes failures proactively, improves maintenance and boosts reliability.
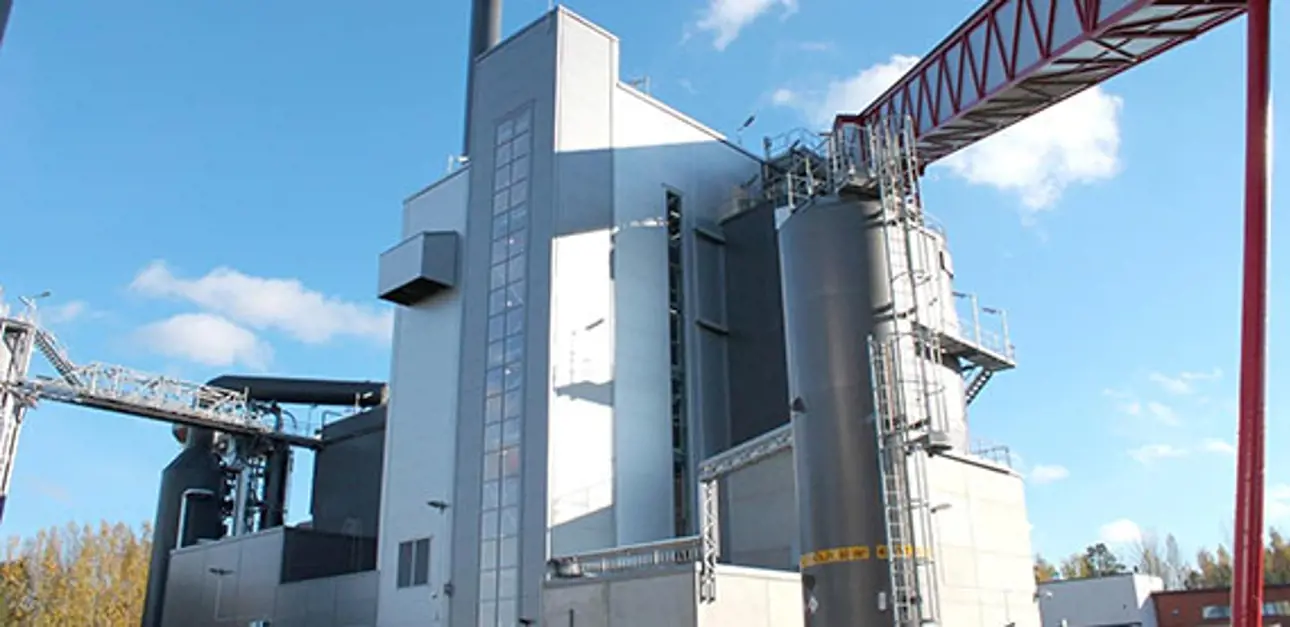
The temperature plummeting down to -20 °C in late November and early December 2021 showed once again the importance of the woodchip-fired plant in Hervanta, a large suburb of Tampere, Finland. The district heat it produces keeps the homes of approximately 20,000 residents warm.
Supplied by Valmet in 2015, the 45 MWth unmanned base-load power plant is annexed to the local district heating grid and operated remotely from a control room at the Lielahti plant on the other side of the city through Valmet DNA Automation System.
“We run the plant from nine to ten months per year, mostly at full capacity. Even though it is merely a heating plant, it plays a major role in our company’s cost structure. That’s why we wanted to invest in its availability. We aimed to proactively observe any emerging limitations step by step and recognize as maintenance needs developed. This would enable us to react as early as possible,” explains Jari Pinomäki, Production Manager at Tampereen Sähkölaitos.
The company has cooperated closely with Valmet in many projects over the past decades. Its plants utilize Valmet’s energy production technology extensively, and all of its plants are operated with Valmet’s process automation and information management systems.
Valmet had a suitable concept on which we were able to build a working solution to meet our needs.
“Our target is to develop our digitalization capabilities further and be aware of the plant condition online. After evaluating various alternatives from many different suppliers, we chose Valmet. It had a suitable concept on which we were able to build a working solution to meet our needs,” Pinomäki continues.
Prior to defining the solution contents together, the customer and Valmet checked the condition of the critical equipment and the need for new online measurements.
Data goes to the Valmet cloud
In June 2021, Valmet commissioned a solution that included five VII reliability and performance applications to analyze the condition of the Hervanta plant. These included:
- Condition Monitoring
- Equipment Diagnostics
- Control Performance
- Centerline Advisor
- Energy KPI Monitoring
To monitor the process and mechanical status of the plant, the delivery included new pressure, temperature and vibration sensors and measurements. Via a remote connection from the plant’s automation system, the data collected goes to the Valmet cloud, where it is analyzed.
The parties signed a service agreement that ensures on-demand support from Valmet Performance Center (VPC), quarterly process reporting as well as platform support and future upgrades.
When in doubt, Tampereen Sähkölaitos can turn to the VPC for expert support through the customer portal. Chatting with Valmet’s experts offers an easy way to discuss any issue. They are able to quickly diagnose the situation by utilizing plant data stored in the cloud.
“Cooperation with Valmet has been smooth. Every time I have contacted the experts, they have responded swiftly,” says Jyri Isokivijärvi, Operations Engineer. He is in charge of the company’s heating plants and is an active user of Valmet’s VII applications.
To improve usability, Valmet developed a front page for the operations panel – a dashboard – to visually present results from all applications, including KPIs and alarms from the most important changes. Now it is possible for all user groups to see the overall plant situation at a glance. The dashboard shows what is going on with the VII applications. This information boosts proactivity and enables Tampereen Sähkölaitos to focus their maintenance actions correctly.
Digging deep into the plant’s psyche
In mid-December 2021, Tampereen Sähkölaitos had been using Valmet’s maintenance-related VII applications for about half a year.
Just by catching one major equipment failure in advance, we can cover our investment price.
“As the plant is still relatively new, there have been no equipment failures so far. However, we have been able to tap into some upcoming failures that would not have come to our knowledge with our old tools,” Isokivijärvi remarks. “Since I started using the applications, I have been able to dig deeper into the plant’s psyche from the controllers that guide me to continue in some particular direction. Sometimes, I get almost carried away – and wish I had more time to look into the proposed options.”
Isokivijärvi has been especially impressed by the Equipment Diagnostics tool. According to him, it shows all changes in equipment status at a glance in a very visual way. This makes it easy to start looking for reasons for the change. He continues: “Just by catching one major equipment failure in advance, we can cover our investment price. Finding defects that could lead to possible equipment failure brings us the greatest benefit.”
We need more of these kinds of applications to inform us about the plant status.
Jari Pinomäki agrees with him and emphasizes the future opportunities and benefits brought by digitalization to plant maintenance. “We need more of these kinds of applications to inform us about the plant status. They indicate when something is changing in the process and give us input to check the changes. In a way, they rationalize our work by enabling us to concentrate on solving the problems instead of on the equipment that is running well.”
For more information about the VII applications, go to VII solutions and remote services for energy.
Text: Marjaana Lehtinen
Related articles