ARAUCO MAPA project - Building the future mill
Apr 24, 2020
ARAUCO’s major expansion project in Chile - MAPA – is being constructed with a good pace. Once completed, the mill will focus on producing high-quality pulp and renewable energy. Advanced technology will secure efficient processes for years to come.
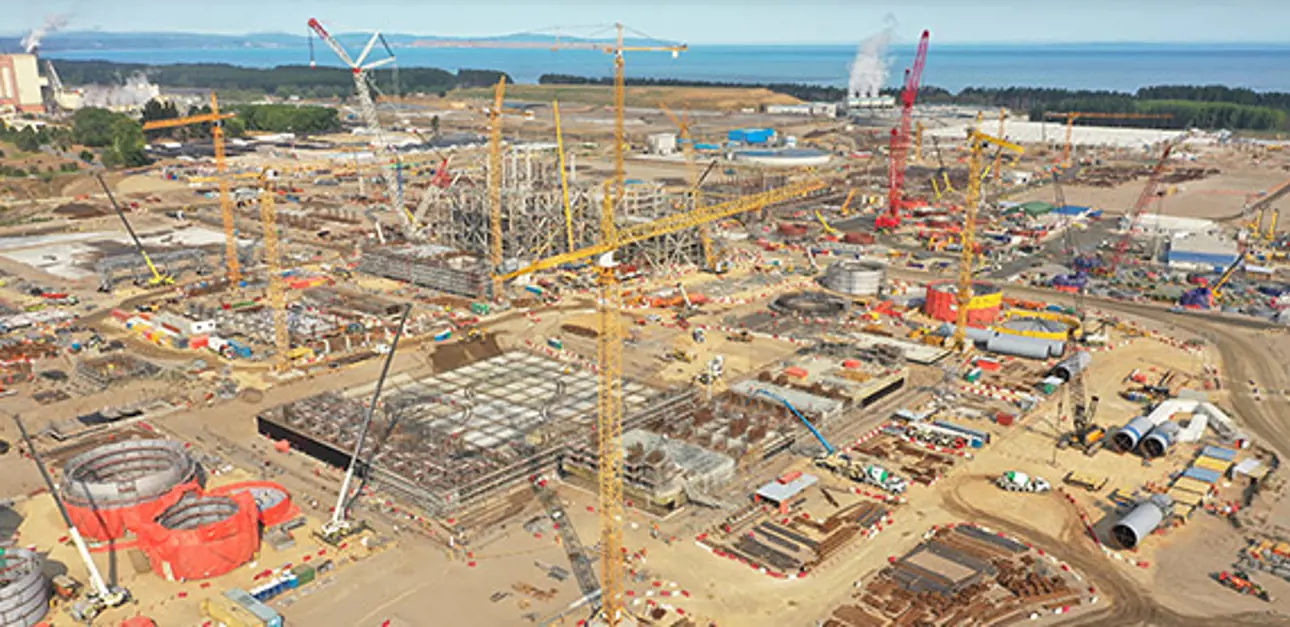
The Arauco Mill is located just off the shores of the Pacific Ocean at the foot of the Andes in Horcones, Chile. In 2018, ARAUCO decided to initiate a major investment project to expand the mill’s pulp production with a new 1.56 million tonne eucalyptus pulp production line and the modernization of the existing 0.55 million tonne radiata pine pulp production line. The project is called MAPA, an acronym for Modernización y Ampliación de Planta Arauco – Modernization and Extension of Arauco Mill in Spanish.
“MAPA is the largest industrial project in the Biobío region, and one of the most important in Chile. It’s also the largest and one of the most important investments in ARAUCO’s history – with an investment of 2.35 billion dollars, 30 months of construction and an expected employment impact of more than 8,000 jobs,” explains Charles Kimber, Senior Vice President of Corporate and Commercial Affairs at ARAUCO.
“This investment establishes us as one of the most important producers of eucalyptus pulp worldwide. In addition to high-quality pulp, the expansion project will allow us to increase the generation of clean and renewable energy from forest biomass,” adds Franco Bozzalla, Vice President of Pulp and Energy Business at ARAUCO.
Franco Bozzalla, Vice President of Pulp and Energy Business at ARAUCO (left) and Charles Kimber, Senior Vice President of Corporate and Commercial Affairs at ARAUCO
Securing the most efficient processes
Valmet was chosen to deliver pulp drying and baling lines, a recovery boiler and a biomass boiler for the project. The delivery project was kicked off in late 2018, and it is planned that the new mill will commence operations in second quarter of 2021.
“We know that Valmet has the best technology in the world for our field, and we wanted the best of the best for our new line. We’ve worked together with excellent results and service for many years. We want to secure the most efficient processes, improve environmental efficiency, waste less water, use fewer chemicals and all in all get the most out of wood – and for that, we always knew that Valmet was an excellent choice. Works are proceeding and by the end of January 2020 the project had a completion rate of 35.5 percent,” Bozzalla summarizes.
“Our customer started the site works in early 2019, and they’ve done the engineering and most of the production and procurement for the key technologies. Our site team is in place, and several shipments have arrived at the site. This year will be very busy, with finalizing the final procurement and shipments to the site, and supervision of the installation of our equipment,” says Paulo Aguiar, Vice President, Wood and Pulp Handling business unit at Valmet.
Valmet Cutter was preassembled in Ulvila Finland before shipment to Chile.
The boiler feedwater tank, with a length of 38.5 meters and empty weight of nearly 200 tons, was manufactured in Estonia.
Predictive pulp drying production
The pulp drying line consists of two complete drying machines, including four high-capacity baling lines. The pulp drying line will allow continuous high-quality production. It will also include low-energy and heat-consumption technologies, contributing to a lower operational cost and minimal environmental impact.
“We’ve delivered three drying lines to ARAUCO previously, so the MAPA delivery is a repeat order, and these will be the fourth and fifth drying machines we’ve delivered to them,” says Aguiar.
Paulo Aguiar, Vice President, Wood and Pulp Handling business unit at Valmet
The drying machine will be equipped with the most advanced process controls to automatically adjust the production parameters and achieve high availability, with minimal need for human operations.
“It will be predictive production by advance bale weight control. We’re installing sensors that will support the customer remotely. A web monitoring system, scanners and profiling will all contribute to the good runnability of the machine.”
In addition to the high automation of the drying machine, expert support will also be available if required to support Arauco’s operators via a remote Internet connection from Valmet Performance Center and process analysis through Industrial Internet applications.
Renewable energy from the forest
“The expansion project will allow our mill to increase the generation of clean and renewable energy from forest biomass. The recovery and biomass boilers will supply clean energy to the mill, and an energy surplus of 166 MW will be delivered to the Chilean National Electrical Grid,” Bozzalla says.
The recovery boiler includes Valmet’s advanced high-power features, enabling maximum energy efficiency and high electricity production, and a smelt spout cleaning robot for improved safety and operator-friendliness.
The power boiler is tailored to burn local biomass, such as eucalyptus bark, chipped wood, wood residue and effluent sludge. Both boilers are equipped with Valmet ESPs (electrostatic precipitators) for excellent dust particle removal from flue gases.
“Our boiler delivery is a truly multinational effort. The key design, engineering and production of key components come from our home base in Tampere, but Valmet teams in other locations in Finland, Sweden, India, China, Brazil and – naturally – Chile are contributing in their area of expertise,” says Tapani Nummelin, the Project Manager for the Valmet boiler delivery.
Tapani Nummelin, the Project Manager for the Valmet boiler delivery visiting the Arauco MAPA site in January 2020.
Valmet will also deliver the mill-wide NCG (non-condensable gases) collection and handling solution to secure safe incineration of the odorous gases formed in the pulp production process.
Extra effort for local circumstances
Chile and its pulp production facilities are in a seismically active region. The strongest known earthquake of modern times, the 1960 Valdivia earthquake, was recorded in Chile. In March 2010, an earthquake severely affected Central Chile and the entire pulp and paper production of the country. As a result, new regulations and procedures were put in place for construction that also impacted the boiler design for this project.
“This was the first new pulp mill to be built in the region after the 2010 earthquake. Our calculation was affirmed by the leading Chilean seismic expert, Professor Rodolfo Saragoni. Naturally, this was something new for us, but it was great to see how the experts from both sides worked together, and kindred spirits were found,” Nummelin explains.
The result is that the recovery boiler steel structure weighs about 50 percent more compared to a boiler build of similar size elsewhere in the world.
Text Kerstin Eriksson, Lotta Forssell, Francisca Maass
Scope of Valmet's delivery
- Pulp drying line with a daily capacity of 5,000 Adt and the potential for future capacity increase through debottlenecking: 2 drying machines and 4 high-capacity baling lines
- Recovery boiler with a daily capacity of 6,300 tDS with a smelt spout cleaning robot
- Fluidized bed power boiler with a capacity of 160 MWth
- Mill-wide NCG collection and handling solution
Related articles