Reducing the OPEX of lignin production
Dec 5, 2024
Valmet’s Lignin Mill concept ensures a comprehensive approach to the pulp mill’s chemical and energy balance, enabling a reduction in the operating expenses of lignin production.
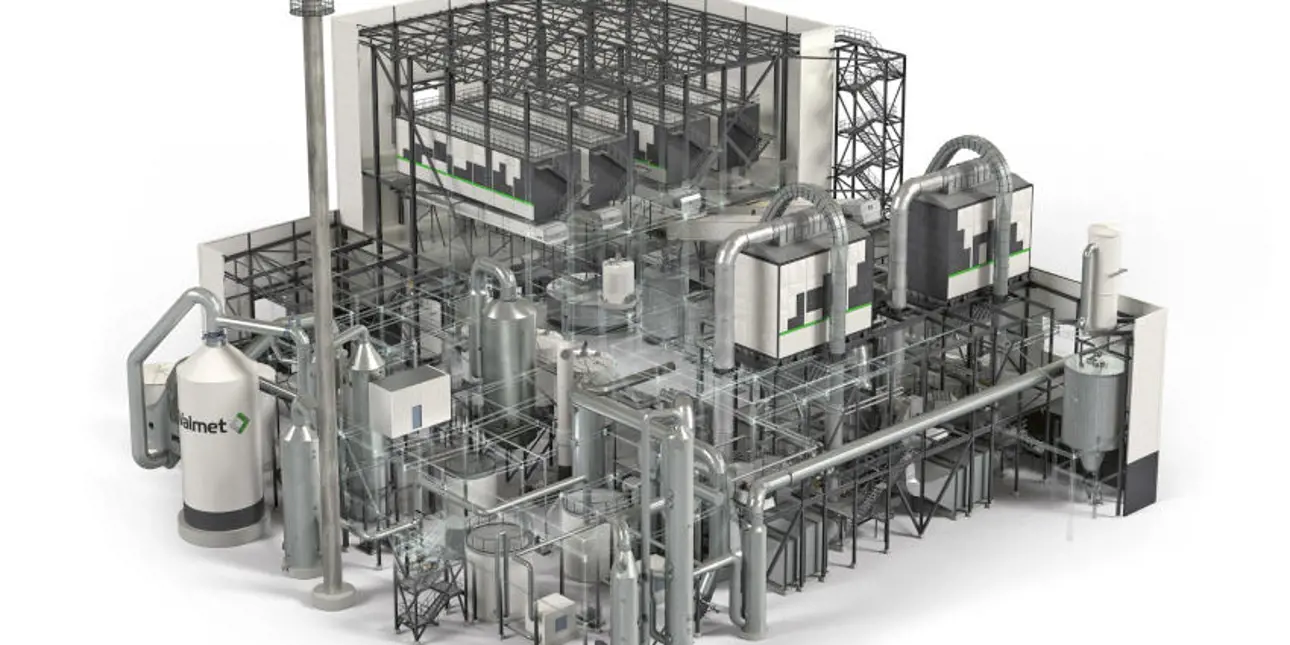
Global trends are boosting the demand for new biobased materials. Lignin is nature’s own organic polymer which can replace several different fossil-oil-based materials, creating a new business opportunity for chemical pulp mills.
“Lignin is a valuable raw material that has many uses. Instead of burning all the lignin in the recovery boiler, there’s increasing interest in utilizing some of this lignin for higher-value products to bring additional revenue streams to the mill. Kraft lignin production with Valmet LignoBoost® technology has been one of our key biomaterial development areas for over a decade. We have delivered two small-scale LignoBoost XS plants and two larger-scale LignoBoost plants, and we're continuing to take the industry forward with the experience we've gained,” explains Jussi Mäntyniemi, Vice President for Recovery at Valmet.
The Valmet Lignin Mill uses a combination of proven technologies.
Valmet’s Lignin Technology Business Development Manager, Hanna Karlsson, explains the basics behind the new approach to lignin production: “As with any investment, the target is to optimize both the investment and operating costs. With our extensive process knowledge, we’ve been able to develop a comprehensive Lignin Mill concept.”
![]() |
Hanna Karlsson, Business Development Manager, Lignin Technology, Valmet. |
Reducing costs and emissions
Lignin production requires sulfuric acid to purify the lignin. This creates a challenge with sulfur management in the mill’s chemical cycle. The Valmet Sulfuric Acid Plant is an excellent solution that prevents the increase of sulfidity in the process.
“Valmet’s integrated sulfuric acid plant solution produces sulfuric acid from the mill’s own sulfurous gases. These concentrated non-condensable gases (CNCGs) are collected from the fiberline and evaporation processes. Additional sulfur separation may be necessary if large-scale lignin production is planned. Depending on the required amount, this can be done with green liquor stripping or black liquor heat treatment. If needed, elemental sulfur can also be utilized in sulfuric acid production,” explains Jaakko Jägerroos, Chief Engineer in Valmet’s Mill-wide NCG solutions team.
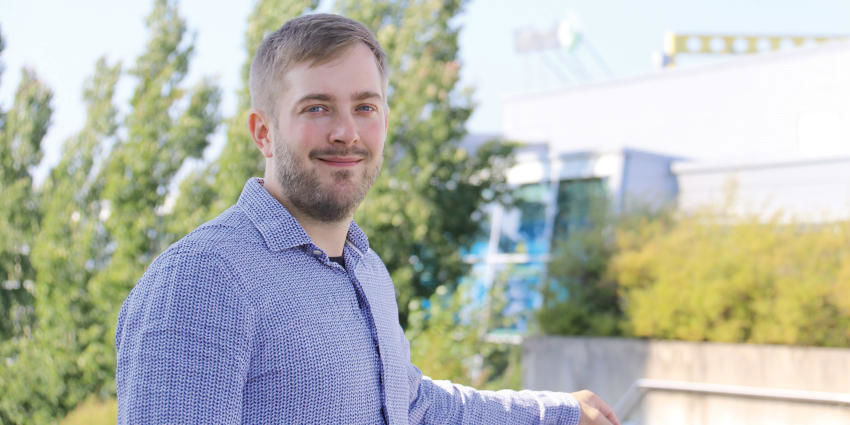
Jaakko Jägerroos, Chief Engineer in Valmet’s Mill-wide NCG solutions team.
“Removing the excess sulfur from the mill cycle reduces the need for ash dumping. In turn, this reduces the need for make-up sodium. Ultimately, comprehensive sulfur management both reduces operating costs and improves the mill’s environmental performance,” he adds.
Valmet’s lignin mill concept enables value-added lignin production and is fully integrated with the pulp mill.
Bringing technologies together in a new way
Hanna Karlsson emphasizes that Valmet’s extensive technology experience has resulted in a robust concept. “With this concept, we’ve combined technology solutions that are all proven in practice. In addition to lignin and sulfuric acid production, lignin’s physical properties may need to be tailored to meet specific end-product requirements or logistical needs. For example, lignin can be provided in various dryness levels and formats such as powder or granules. In collaboration with our partners, we offer drying, conversion, storage, and packaging solutions to address these needs,” she adds.
“Every mill is different, and the process needs to be tailored for each case. We also need to remember that lignin production may affect other parts of the pulp mill, especially the recovery island. This is never a plug-and-play solution, but a complex puzzle that needs the close cooperation of various process experts,” Jaakko Jägerroos says.
Tailoring lignin for different end uses
Hanna Karlsson has worked for more than 15 years with Valmet’s LignoBoost development, helping customers find their way into this new business area. “We can offer chemical pulp producers considering starting kraft lignin production a roadmap for their investment journey. Normally, we start with studies, including laboratory tests. We also have a container-sized pilot unit that is traveling around the world as we speak. For customers who want to start more in-depth lignin development, we have a small-scale plant, LignoBoost XS, which we’ve already delivered to two customers.”
Valmet is developing the production of various lignin qualities.
“We have several concepts for tailoring lignin qualities for specific use cases. For example, we have developed UltraPureTM and OdorFreeTM qualities. These aren’t just laboratory studies – they’re ready for commercialization. As we have more than a decade’s experience of industrial scale lignin production, we have a good understanding of the necessary lignin properties and possible end uses. Moreover, we collaborate with different companies along the value chain to ensure our solutions meet market demands,” Hanna Karlsson concludes.
Text: Lotta Forssell
Photos and illustrations: Lars Berggren, Andreas Liedberg, Lotta Forssell, Stora Enso
What is lignin?
Lignin is a natural and renewable polymer found in the cell walls of plants, where it binds cellulose and hemicellulose together. Trees have a lignin composition of 20–30 percent, and most of the lignin in kraft pulp production is dissolved into black liquor.
Related articles