Service Agreements for Optimized Performance
Oct 17, 2024
In today’s competitive industrial landscape, fiberboard manufacturers are constantly looking for ways to enhance operational efficiency and reduce downtime. This drive for optimization has led many companies to explore service agreements that ensure long-term equipment performance and reliability.
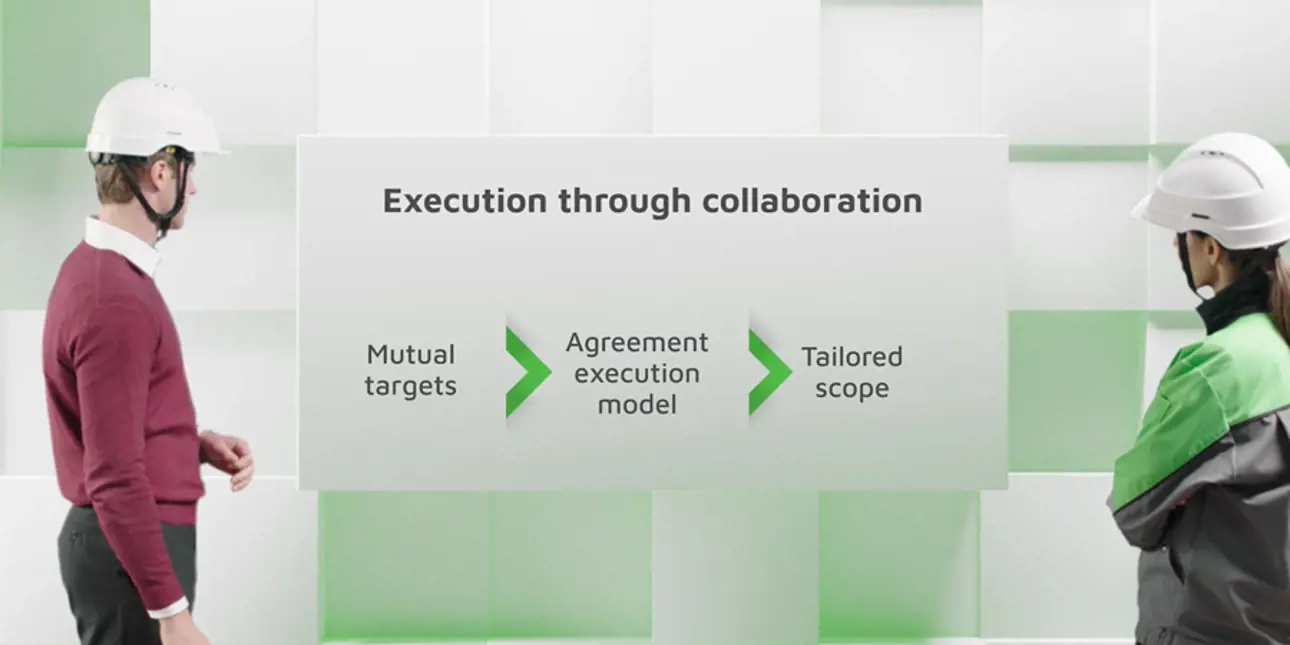
Valmet, a global leader in fiberboard production solutions, offers tailored service agreements designed to help manufacturers achieve these goals. In this article, we will delve into why service agreements are crucial for fiberboard manufacturers, explore the types of agreements Valmet offers, and provide examples of the concrete benefits these agreements deliver.
What types of Service Agreements does Valmet offer?
Valmet offers a wide range of service agreements that cater to the diverse needs of fiberboard manufacturers. Each is designed to address specific challenges within a plant, whether it’s improving performance, ensuring uptime, or reducing operational costs.
1. Maintenance and Lifecycle Services
Valmet’s maintenance agreements focus on preventive care, ensuring that equipment is regularly inspected, maintained, and optimized for performance. Lifecycle services, on the other hand, provide comprehensive support throughout the entire lifespan of equipment, from installation to upgrades and eventual decommissioning.
2. Condition Monitoring and Predictive Maintenance
These are ideal for manufacturers looking to minimize downtime. Using advanced sensor technologies and Valmet’s Industrial Internet solutions, condition monitoring agreements allow manufacturers to detect early signs of equipment wear and tear, enabling timely repairs before major issues arise.
3. Performance Optimization Services
For manufacturers looking to maximize output while maintaining quality, Valmet’s performance optimization agreements offer ongoing support for improving production processes. This includes upgrades to existing systems, process fine-tuning, and continuous monitoring to ensure optimal efficiency.
Why Are Service Agreements Important for Fiberboard manufacturers?
Fiberboard production involves complex machinery and processes that need to operate continuously and efficiently. Unplanned downtime, equipment failures, and inconsistent performance can all lead to significant financial losses and production delays. Service agreements are essential for fiberboard manufacturers because they provide ongoing support that ensures the long-term reliability of production equipment.
1. Reduced Downtime
One of the most critical aspects of any manufacturing operation is keeping the equipment running as efficiently as possible. With Valmet’s service agreements, fiberboard manufacturers can rely on preventative maintenance and real-time monitoring to catch issues early before they lead to costly downtime.
2. Enhanced Performance
Service agreements also ensure that machinery is continually optimized for performance. Valmet’s performance optimization services provide regular assessments and fine-tuning, ensuring that fiberboard manufacturers can consistently produce high-quality products while reducing raw material and energy waste.
3. Cost Predictability
Rather than dealing with unexpected repair costs, service agreements provide fiberboard manufacturers with more predictable operating expenses. By investing in a long-term maintenance plan, companies can avoid sudden, large expenses associated with major equipment failures.
What are the gains from Service Agreements?
Fiberboard manufacturers that enter into service agreements with Valmet gain access to a range of benefits that go beyond just operational reliability. These agreements are tailored to meet the specific needs of each customer, ensuring that they receive the maximum return on their investmen.
1. Access to Valmet’s Global Expertise
With service agreements, fiberboard manufacturers tap into Valmet’s extensive network of industry experts. Valmet’s Performance Centers provide remote support and diagnostics, ensuring that any issues are addressed quickly, no matter where the customer is located.
2. Proactive Problem Solving
Rather than reacting to issues as they arise, service agreements provide proactive solutions. Through predictive maintenance and real-time monitoring, fiberboard manufacturers can anticipate problems and take corrective action before they affect production.
3. Improved Safety and Compliance
Service agreements also ensure that equipment is operating safely and in compliance with industry standards. Regular maintenance checks help identify any safety issues before they become serious, providing peace of mind to manufacturers.
An example from one of our customers:
One fiberboard manufacturer reported a significant improvement in safety after entering into a service agreement with Valmet. By conducting regular safety inspections and equipment assessments, the manufacturer was able to maintain compliance with regulatory standards, reduce incidents, and improve overall workplace safety.
How to Get Started with a Valmet Service Agreement
If you’re a fiberboard manufacturer interested in improving operational efficiency, reducing costs, and enhancing the safety of your plant, getting started with a Valmet service agreement is easy. Here’s how you can begin the process:
1. Assess Your Needs
Before entering into a service agreement, it’s essential to assess the specific needs of your fiberboard production facility. Valmet offers customizable agreements, so understanding what type of support your operation requires will help ensure the right services are included.
2. Consult with Valmet’s Experts
Once you’ve assessed your needs, the next step is to consult with Valmet’s team of experts. They will work with you to design a service agreement tailored to your production goals, ensuring that you receive the best possible support.
3. Review and Sign the Agreement
After the consultation, Valmet will provide you with a detailed proposal outlining the services included in your agreement. Once you’ve reviewed the terms and are satisfied with the offer, you can sign the contract and begin reaping the benefits of continuous support and optimization.
Conclusion
For fiberboard manufacturers, operational efficiency and equipment reliability are critical to maintaining a competitive edge. Valmet’s service agreements offer tailored solutions that help manufacturers reduce downtime, improve performance, and achieve long-term cost predictability. Whether through preventative maintenance, condition monitoring, or performance optimization, Valmet’s global expertise ensures that fiberboard manufacturers receive the best possible support for their production goals.
If you're ready to explore how a Valmet service agreement can benefit your operation, reach out to our team today to start a conversation. Read more about Service Agreements.
Are you ready to succeed with us?
Our experts are here for you and ready to discuss your challenges. Answer a few questions and we will contact you shortly.
Contact us