Together for a safer workplace
May 24, 2024
A safe working environment is at the core of Stora Enso and Valmet’s operations. To further improve their safety performance, Stora Enso and Valmet initiated a joint safety project in 2023. As a result, the companies introduced a collection of best practices to provide a safe workplace during shutdowns and other projects.
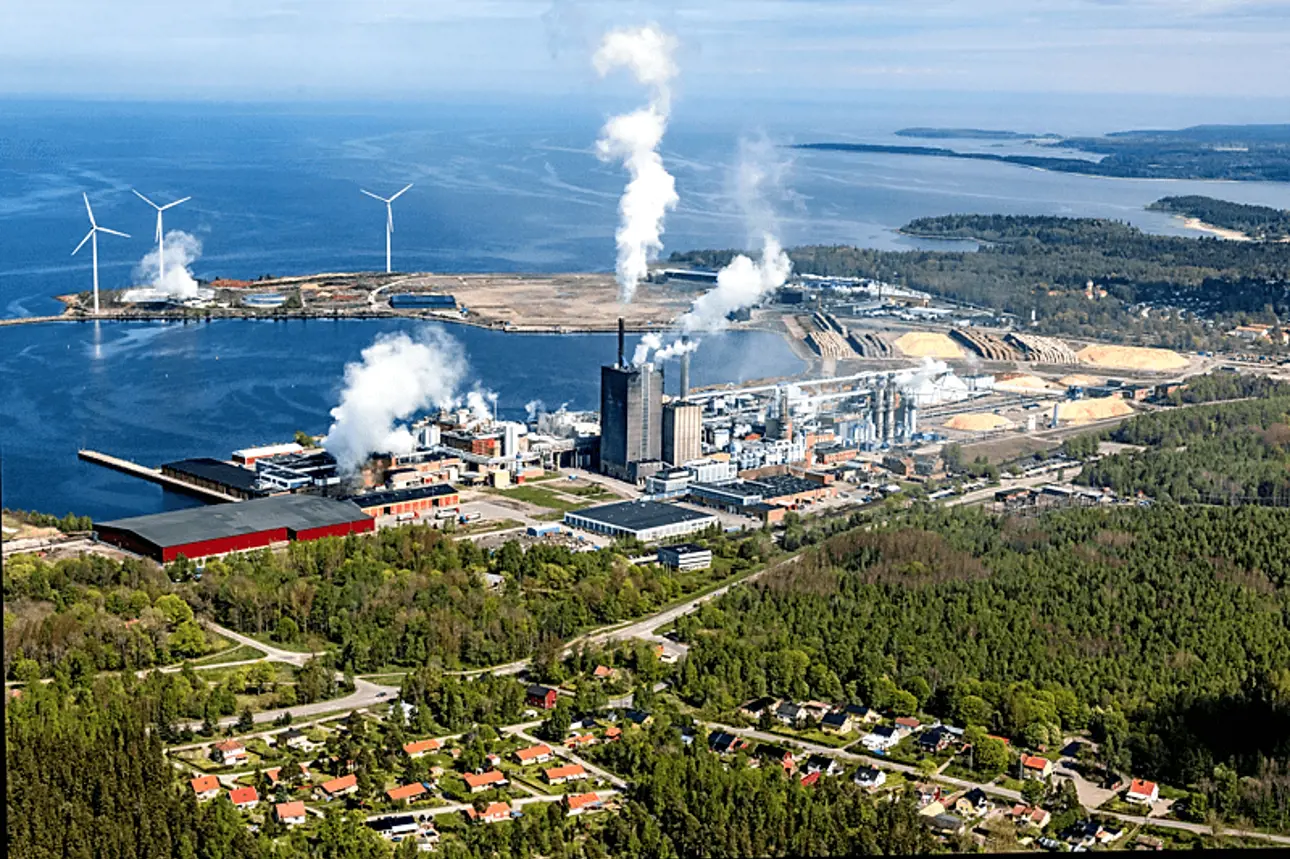
Stora Enso Skutskär biomaterials production site in Sweden was founded in 1895. Today, it is a home for over 400 employees and produces fluff pulp for hygiene products as well as pulp for liquid packaging board and specialty paper with an annual capacity of approximately 545 000 tonnes.
The history of Stora Enso Skutskär and Valmet goes back several decades – over the years, Valmet has supported the site through various service agreements, helping to secure trouble-free operation of the entire pulp production line. Together the companies have run several projects to improve the site’s productivity, safety, sustainability and overall performance. This year, the site’s baling line will go through a safety upgrade during the annual shutdown.
“Our cooperation with Valmet has worked really well. We have cooperated with Valmet’s experts and together we have successfully increased health and safety at our unit. Safety is our priority, always,” says Lars Andersen, OHS Manager at Stora Enso Skutskär biomaterials production site.
Case study leads to improved safety performance
To support their continuous health, safety and environment (HSE) development, Stora Enso and Valmet initiated a joint safety project in 2023. The project was kicked off with a case study of safety routines during the Skutskär site’s annual shutdown.
“Our goal was to evaluate safety routines step by step from signing the contract to handover of machinery back to mill operators. This was done on both sides, and the results were shared. As a result, we were able to highlight multiple good practices to be kept on the agenda and shared with other Stora Enso sites and Valmet’s operations too. Of course, we also specified areas which needed development, and planned corrective actions to those,” says Erkko Penttilä, Director, EMEA Health Safety and Environment Operations at Valmet.
The case study focused especially on cooperation between different parties and overall communication of safety routines and expectations.
“The key learning is probably related to scheduling – the shutdown’s safety planning should be started early enough to have time for necessary safety actions before the shutdown. For example, we organized a contractor HSE Day on site, which was a very good way to discuss safety and go through instructions prior to the shutdown. During the shutdown, we also relied on face-to-face communication and gathered for morning meetings and work group specific toolbox talks to keep up the good dialogue and positive safety attitude on site,” describes Rickard Burlin, Site Manager, EMEA Energy, Recovery and Environment Services at Valmet.
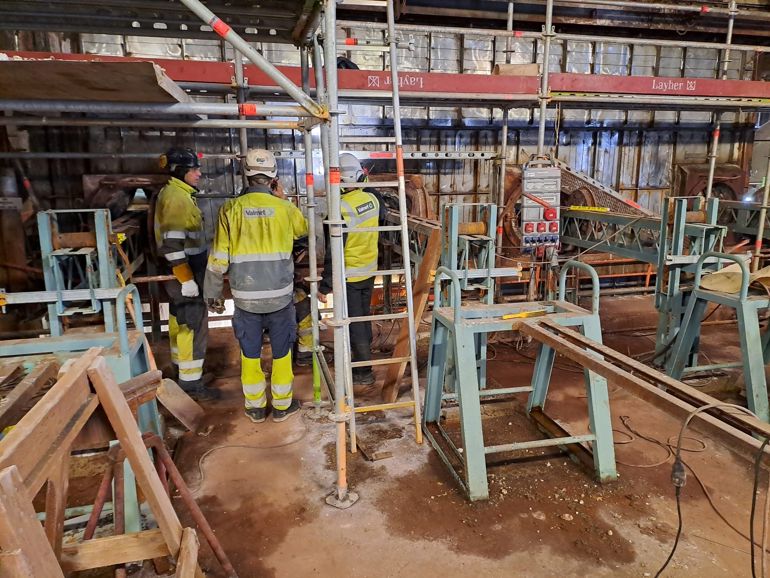
Good cooperation is the key to great results
During an annual shutdown or any other significant project, there are hundreds of people working simultaneously at the site – from Stora Enso’s own personnel to Valmet’s staff as well as to numerous contractors and even their subcontractors.
“To secure an accident-free workplace for all, we need to make sure everyone working at the site is aware of and committed to our safety routines and targets, thus, we need to communicate and cooperate. With Valmet, our cooperation in safety works seamlessly,” Lars Andersen from Stora Enso says.