Is a fully electrified tissue mill a utopian idea?
Dec 4, 2024
Like all other energy-intensive industries, tissue papermaking has been highly reliant on fossil fuels to generate the heat needed for drying. At the same time, in many areas of the world concerns related to climate warming have led to decarbonization policies with stringent deadlines for the industrial sector. In this article we outline how electrification of the drying section of a tissue machine by the means of electrical heaters and high temperature heat pumps can represent efficient and smart ways to decarbonize the tissue making process.
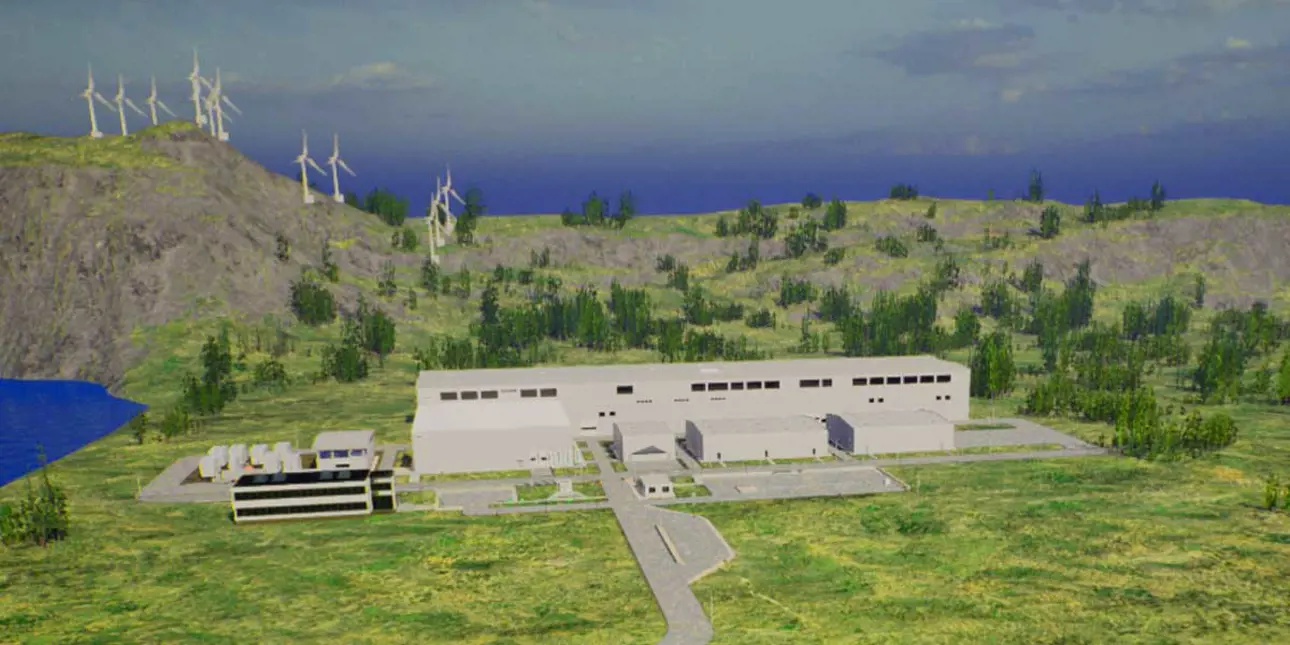
Possible saving coming from the conjunct implementation of Electrical Heater and HTHP on a 5.6 meter wide tissue machine
Energy for drying accounts for approximately 70% of the total energy consumption in tissue papermaking, primarily sourced from fossil fuels such as natural gas, coal or LPG. In recent years, different energy vectors have been developed to tackle the challenge of decarbonization in energy-intensive industries.
Electric heater
At Valmet, we offer a wide portfolio of solutions to exploit these advancements, ranging from hydrogen-ready AirSystem burner to biomass utilization for steam production. However, when technically feasible, direct electrification brings significant advantages in terms of efficiency and competitiveness, both in CapEx and OpEx. This is especially true when considering electrical heaters as replacements for AirSystem burners and high temperature heat pumps to produce steam for Yankee dryers.
Different possibilities to integrate electrical heater in Tissue Mill AirSystem based on type of project, process and space requirement
Pathway to an electrified hood
The adoption of an electrical heater to electrify the Yankee Hood requires no significant change in the drying philosophy, since the blowing speed and temperature are kept the same.
By using electrical heaters, not only can CO2 and other emissions from fossil fuel combustion be avoided, but efficiency benefits can be achieved. This is thanks to the elimination of combustion air utilization, the avoidance of water generation from the combustion process and a better balance of the AirSystem to enhance energy conservation.
Electrical heaters can be flexibly integrated in both new installations and rebuild projects. At Valmet we have studied different options for their positioning in the AirSystem to enhance flexible operation and to maximize the benefits, both as a stand-alone solution for air heating and in combination with other heat sources for air, such as fossil fuels or hydrogen burners.
Decarbonize steam production with unprecedented efficiency
Around 50% of the drying energy in a tissue machine is derived from steam. The traditional way to produce steam rely on the combustion of gaseous, liquid or solid fuel in a boiler. This process is limited by efficiency in the range of 97% to 80%.
In this context, the adoption of a high temperature heat pump can be a game changer thanks its higher efficiency. High temperature heat pumps are devices that recover heat from a low-temperature source, and by consuming electricity to run a compressor, upgrade it to a higher temperature level. The key feature of this machine is that the heat delivered as output is always higher than the consumption of electricity, thus achieving efficiency that for a steam-producing heat pump for a tissue application can range between 200% and 300%.
High Temperature Heat Pump simplified scheme
High temperature heat pump technology has developed at a remarkable pace over the last 10 years and, thanks to upgraded components and working fluids, it can today produce steam up to 20 bar and above.
Tissue mills have been extremely focused on maximizing energy efficiency through heat recovery, especially in the drying section. However, waste heat streams at temperature levels too low to be directly brought back to the mill are still wasted. These streams represent valuable opportunities for high temperature heat pump to exploit and upgrade the heat to a useful level for the drying process. For example, the exhaust air from the Yankee Hood AirSystem, after the conventional heat recovery chain, still has a significant temperature and moisture content to be exploited. In this context, not only will energy be preserved through additional heat recovery, but water will be saved thanks to the additional condensation of the moisture in the exhaust air, which can be reused in the mill’s water system.
An integrated, decarbonized and highly efficient drying section
Today, technologies for the electrification of the drying section are ready for implementation and solutions for their integration in tissue mill have been validated. Over the past year, decarbonization technologies have encountered significant interest from our customer, and we are actively cooperating with them to implement these solutions in the coming months.
A fully interconnected and highly-efficient drying section by means of the HTHP technology
With the integration of a high temperature heat pump that recovers heat from the exhaust air of the AirSystem and produces steam for the Yankee Dryer, the two systems will be interconnected to maximize the plant’s efficiency in terms of both energy preservation and water consumption reduction and with the additional benefit of not producing any kind of direct emission in the steam generation process.
By adopting electrical heater in the AirSystem, energy consumption can be reduced by up to 10% compared to systems using fossil fuel burners. Additional, CO2 emissions can be entirely offset by using renewable electricity produced locally or from the grid.
More on the topic of optimizing drying
Tissue news
Explore our customer success stories and learn more about our full-scope offering in the tissue industry.