Valmet's novel Sleeve roll technology awarded first prize at ATIP Innovation Contest
Dec 16, 2022
Valmet won this year's prestigious 'Palme d'Or' Innovation Award with its novel Sleeve roll technology and Valmet Sleeve Roll Belt. The award was given by the French Paper Industry Technical Association (ATIP). The innovation contest was arranged in connection with the ATIP Conference and Exhibition in Paris, France on December 8-9, 2022.
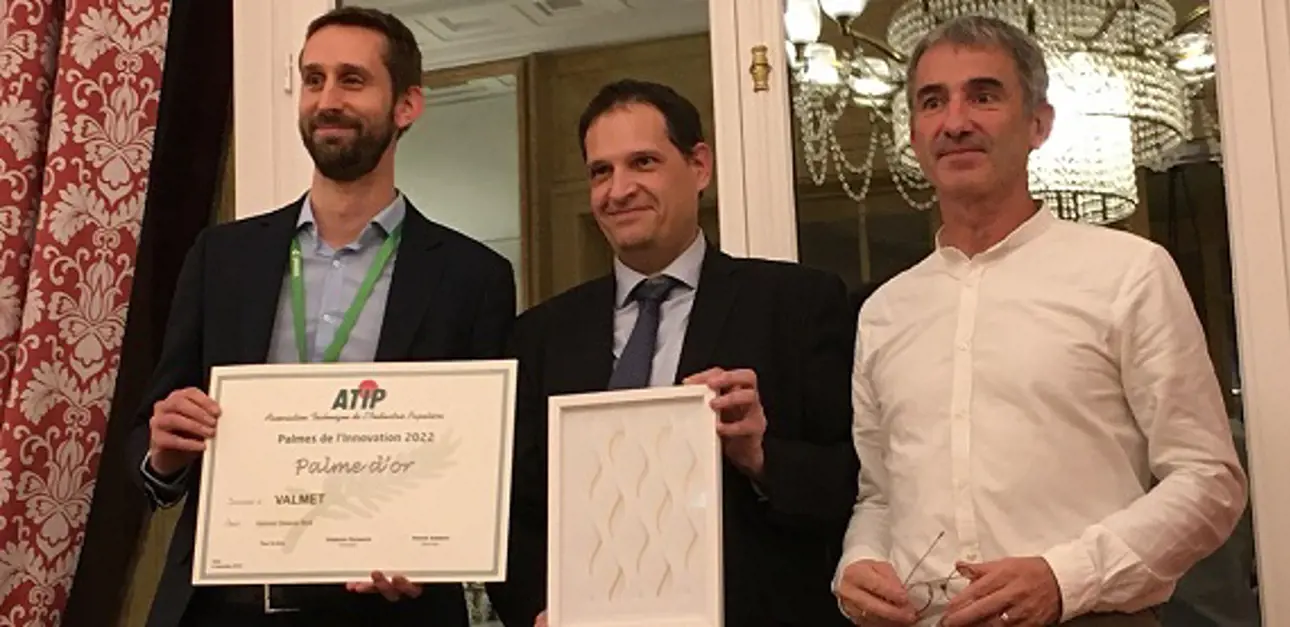
The ATIP Innovation Award rewards innovative equipment and solutions for pulp and paper industry. The award is highly regarded among the European pulp and paper industry, and it is divided into three categories: Gold - Palme d'Or, Silver - Palme d'Argent and Bronze - Palme de Bronze. The ATIP Innovation Award winners are selected by a committee consisting of Paper Mill Managers, R&D Directors, Technology Directors and Production Managers from the French paper industry. The ATIP Innovation Award was established already in 1995.
An innovative idea to act as the North Star, a great team to make it true and a brave customer to be the first. That’s what it takes to bring a new solution like Sleeve roll technology into life. We are proud to have all that is needed to create more sustainable technologies for our customers in the paper industry.”
Sleeve roll technology transforms forming
The forming section is the single biggest user of vacuum energy in a paper/board machine line. Until now the forming section drainage has been relying on gravitation and dragging vacuum elements set along the forming wire travel.
The idea of the novel Sleeve roll technology is that the web is compressed between two forming wires against a small radius shoe and a polyurethane belt is rotating around the roll. Depending on the value of the wire tension and the small radius shoe, we can achieve a very high dewatering pressure level of up to 150 kPa. Dewatering pressure with conventional forming section technologies is typically around 15…40 kPa, and with couch roll or HiVac typically around 60...70 kPa.
As the dewatering with Sleeve roll technology is done with compressing pressure instead of conventional vacuums, Sleeve roll technology does not require vacuum energy, and the power loss due to drag is minimal. Reducing vacuum immediately reduces drive power because of less friction from stationary dewatering elements. Therefore, Sleeve roll will help save energy on both vacuum system and drives, that with conventional technologies constitute approximately 80% of forming section energy usage.
The Sleeve roll needs an elastic and durable polyurethane belt rotating around it. Valmet Sleeve Roll Belt is designed especially for this roll technology where the belt and forming fabric need to work together. The belt responds to the strict requirements regarding, for example, hardness, roughness, and elasticity set for both belt oil side and paper side surfaces.
Innovation is a result of seamless teamwork
Valmet's technology development aims at ensuring advanced and competitive technologies and services, enhancing raw material and energy efficiency, and promoting renewable materials.
"An innovative idea to act as the North Star, a great team to make it true and a brave customer to be the first. That’s what it takes to bring a new solution like Sleeve roll technology into life. We are proud to have all that is needed to create more sustainable technologies for our customers in the paper industry,” says Sampo Immonen, Director, Line R&D, Board and Paper Mills Business Unit.