Time to turn it down
Aug 2, 2019
The remarkable amount of energy that enables the efficient pipeline throughput of oil and gas also carries with it a considerable amount of noise and vibration.
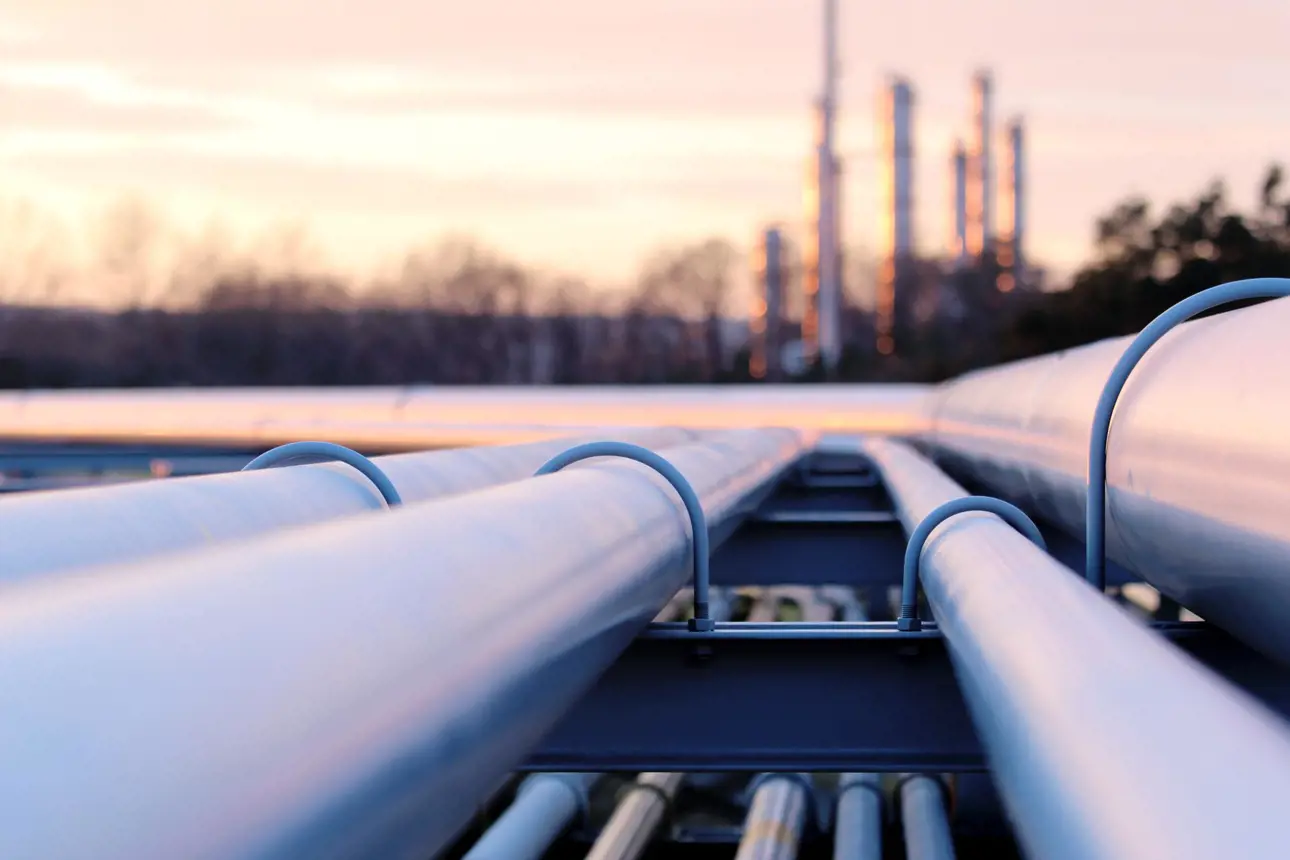
Although unavoidable, noise and vibration are not just a nuisance; they can cause a range of negative outcomes, including some that have the potential to be dangerous.
Oil and natural gas pipelines crisscross North America, constantly moving these perecious resources from one part of the continent to the next with efficiency and precision. In the US alone, there are approximately 95 000 miles of gathering lines and trunk lines as well as countless pieces of equipment that must be maintained in top condition to keep operations safe, efficient and profitable. This is a significant and very complex undertaking, with events and conditions large and small, natural and human-made, that must be taken into account.
Although unavoidable, noise and vibration are not just a nuisance; they can cause a range of negative outcomes, including some that have the potential to be dangerous. For safety, these details truly matter.
While there is no way to circumvent the laws of physics, conditions can be created in which they operate more favourably for operators and the environment. The good news is that managing noise and vibration is not only possible, but also easier and more effective than it has ever been before with the latest technology, putting greater control, safety and efficiency within easy reach.
Hydrodynamic noise – the hidden danger of bubbles
In oil pipelines, dramatic changes in pressure and velocity can result in a phenomenon known as cavitation. Cavitation can become an issue when the pressure of the oil flowing through the valve drops below the vapour pressure, the point at which the oil boils or vapourises. When vapourised, the liquid oil is converted to gas, which materialises as bubbles. This typically happens at the vena contracta, the point of the highest velocity and lowest pressure.
When the velocity of the oil decreases, its pressure conversely recovers until it is above the vapour pressure of the oil (Figure 1). This results in the vapour bubble 'popping', as it implodes and returns to its liquid state. The implosion lasts an infinitesimal amount of time, but in those few milliseconds, a lot of energy is transferred in the form of powerful shock waves. These shock waves are produced because liquid molecules moving at extremely high velocities rush in to fill the voids created as the bubbles collapse. The larger the bubble, and the faster the liquid is moving, the more powerful the shock waves kinetic energy.
In addition to the shock waves of concentrated energy, these implosions also produce powerful microjets of directional energy. These erupt through the surface of the bubbles with unidirectional force that is typically in the millions of psi.
In fact, these bubbles are the root cause of the localised hydrodynamic noise that can be heard in piping systems when cavitation is present. Though usually not overly loud, this seemingly innocent bubble bursting can produce enough power, in the form of shock waves and microjets, to cause significant erosive damage, including mechanical damage to valve assemblies. Therefore, this needs to be addressed with a certain level of urgency.
Understanding aerodynamic noise
Aerodynamic noise generation is caused by supersonic flow velocities. In fluid mechanics, supersonic means a flow of a fluid travels at speeds greater than the speed of sound in that fluid, causing the shock waves to appear.
As a gas flows through a venturi - a restriction in the pipeline - its velocity increases since the same amount of media is pushed through a smaller opening. Figure 2 is a graph of velocity within the venturi. The 'y' axis of the velocity graph has units of Mach number, where a Mach number of 1 means that the flow is at sonic velocity, which is the maximum velocity within the restriction possible for the gas, as well as the speed of sound.
The Mach number is an important parameter to determine the noise level in the valve and also the potential for vibration in the piping system.
At the point of greatest restriction, Mach 1 is the highest velocity that is physically possible. Still, speeds greater than Mach 1 are possible downstream of the restriction.
As velocity continues to increase through the venture, a point is reached where the downstream velocity exceeds Mach 1. The propensity of gas velocity is to remain below the speed of sound. So, downstream of the venturi, the velocity will suddenly drop back to Mach 1 or lower. This near-immediate and dramatic change in velocity and pressure occurs in a space the width of only a few gas molecules and produces a powerful shock wave, causing extreme turbulence. This is compounded by the tendency of shock waves to 'attach' to physical boundaries, where they take on complex and interacting shapes, creating even greater turbulence.
Reducing cavitation, noise and vibration
Noise and vibration can shake up every part of operations through unplanned maintenance costs, replacement of vital parts, lost uptime, missed revenue and other problems. In addition, noise and vibration present significant issues in both safety and community relations. Even the safest operation is not successful if it is loud enough to be disruptive to the surrounding community.
Neles™ Q-Trim control valves are suited for oil pipelines and equipped to reduce noise and vibration, with features based on knowledge from 50 years of expertise (Figure 3). Some of the ways that Q-Trim is designed to solve pipeline problems include:
-
Pressure stagging to reduce or eliminate cavitation: The Q-Trim attenuator plates stage pressure drops into multiple, smaller pressure drops, preventing or mitigating the massive pressure drops that cause cavitation - and the resulting shock waves, microjets and attendant destruction.
-
Flow division for quieter, safer throughput: By dividing the flow into multiple streams, the intensity of the noise generated by a single orifice decreases rapidly as the diameter of the hole narrows down. This means that a number of smaller holes attenuate noise more effectively than just one big hole. A rule of thumb is every time the number of holes is doubled, the noise is reduced by 3 dBA.
-
Variable-resistor design for greater control over pressure and noise: Q-Trim's variable-resistor design puts the entire solution inside the valve, optimising pressure flow and helping to reduce noise by up to 15 dBA. Fixed-resistor designs have little effect on minimum flow rates, where larger differential pressures are generated, creating cavitation and noise.
-
Peak frequency shifting for less vibration: Lower frequencies produce larger wavelengths, which travel more easily through matter. This means that, like loud bass emanating from a car speaker, the lower frequencies generated in a valve can become a nuisance for people in quiet residential areas. Spectral analysis of noise levels in control valves with Q-Trim technology versus those without it shows that Q-Trim has a significant advantage in reducing both noise and vibration (Figure 4).
-
Self-cleaning valve trim for maximum reliability: Q-Trim uses process media to flush build-up away from the attenuator plates as the trim rotates. This keeps the valve in peak working condition, bringing considerable cost savings each year and giving greater control over process variability.
Conclusion
Dealing with severe piping system noise from control valves is still a problem for many pipelines. However, thanks to dedicated R&D effort, advanced technology exists to make this problem an issue of the past.
Quarter-turn control valves with Q-Trim technology are designed to reduce noise and vibration, enabling pipeline operators to ensure safe, efficient and compliant working conditions while simultaneously protecting the environment.
Through smart science that takes every detail into account and smart design that turns ideas into action, such technological advancements like Q-Trim valves, which are suited for oil and gas pipelines, can help companies to create more efficient and reliable operations.
Text by Steven Hocurscak. For additional information, please contact joonas.korhonen@valmet.com.
This article was originally published in World Pipelines magazine August 2019 issue.
The text has been updated in April 2022, due to the company name change to Valmet.

Subscribe to our newsletter
Subscribe now to flow control newsletter and receive the latest insights directly to your email.
SubscribeRead more about Q-Trim and innovation at Neles