Deaeration
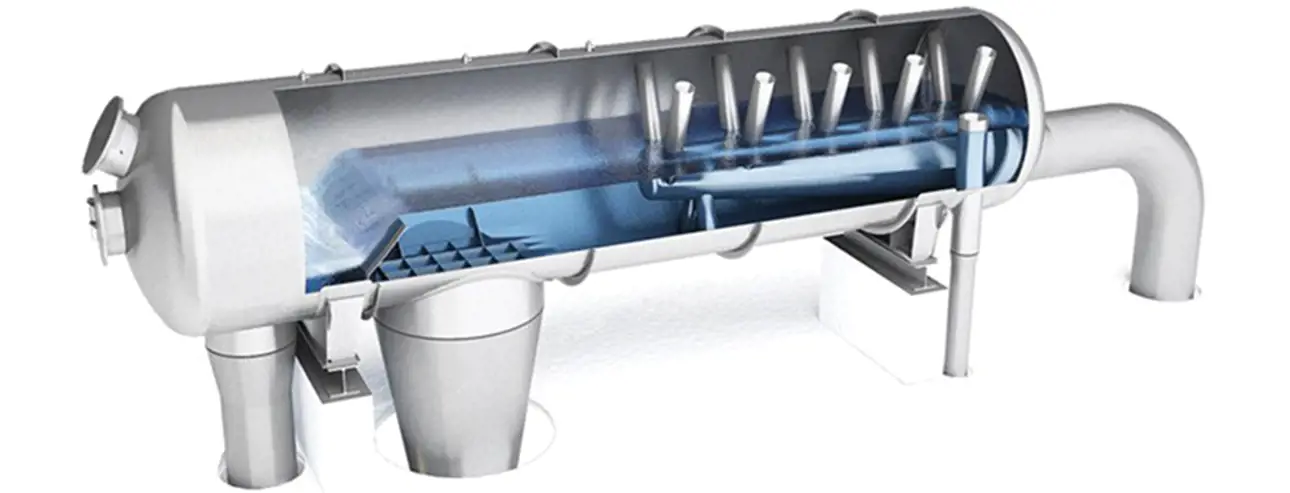
Enhanced efficiency
Reduced cost
Eliminates pressure and consistency variations
Efficient air removal from stock
Valmet offers both passive and active deaeration solutions to meet the varying needs of every papermaker, designed for different paper and board grades and forming concepts. Deaeration refers to the removal of air. The air in the stock can have negative effects on downstream equipment and the quality of the final product.
Passive Deaeration
Valmet Flume wire-water channel removes free air and other gases from the wire water more efficiently than a conventional wire water silo. Developed to meet the challenges of higher gas content resulting from high-speed forming sections, Valmet Flume enhances papermaking efficiency as a pre-deaerator before a deaeration tank or as the only deaerator where vacuum deaeration is not required. By reducing process volume, deaeration facilitates faster process changes resulting in lower costs related to grade changes.
Active deaeration
Active stock deaeration is needed on all high-speed paper machines and is recommended in fourdrinier and hybrid machines in which mechanical pulp and calcium carbonate fillers are used. The Valmet Deaeration Tank ensures maximum free and dissolved gas removal efficiency when treating wire water or headbox stock. By eliminating pressure and consistency variations and providing the paper machines with clean stock, Valmet Deaeration Tank ensures stable process conditions for targeted paper quality. Stock or wire water is fed to the vacuum deaeration tank where virtually all dissolved gas and gas bubbles are boiled off. To intensify the deaeration process, stock or wire water is sprayed through jet nozzles onto the roof of the tank thereby enlarging the gas removal surface area.