A milestone in digital transformation
Dec 5, 2024
Irani Papel e Embalagem S.A. selected Valmet DNA Distributed Control System (DCS) to modernize the reliability and productivity of their Vargem Bonita paper mill and created a new way of operating.
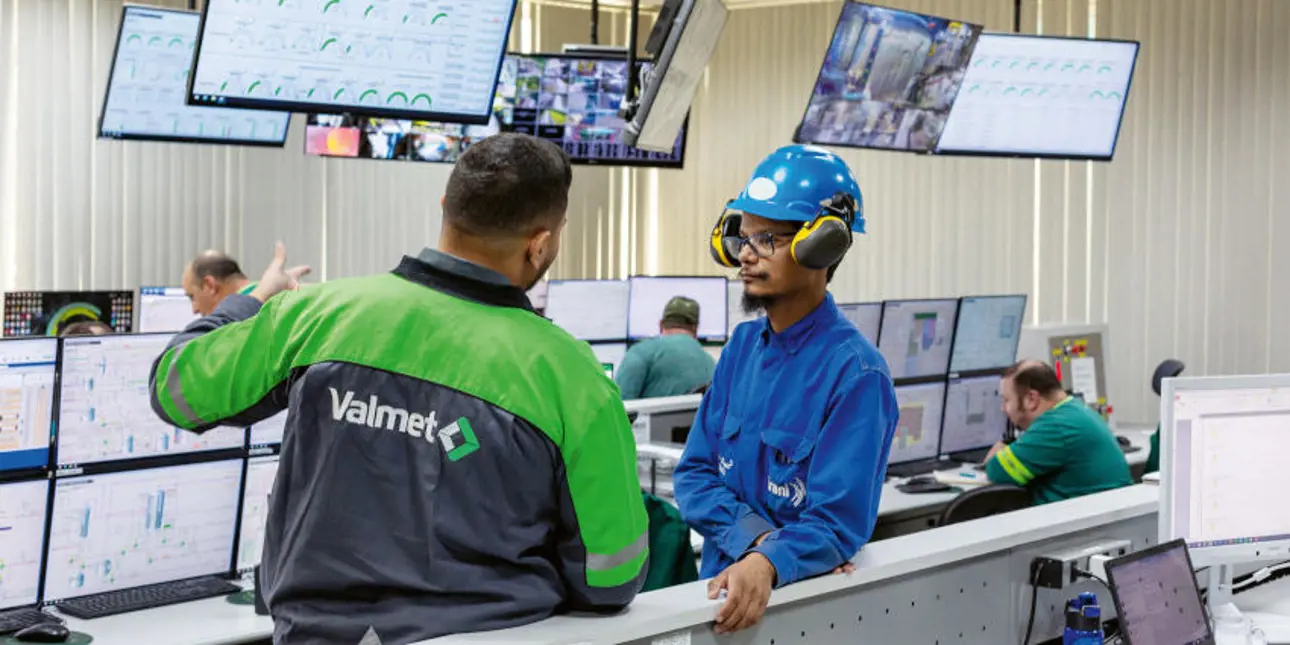
The new DCS is a turning point in how the Irani mill is operated.
The successful implementation of the Distributed Control System (DCS) at Irani Papel e Embalagem S.A. represents an important milestone in digital transformation at the Vargem Bonita mill in southern Brazil. The project was motivated by the need to modernize and expand both production and the chemical recovery at the mill.
“We were able to unify everything into a single system,” says Hernandez Camargo, Automation Coordinator at Irani.
Safe and successful implementation
The Vargem Bonita mill is a brownfield site, and the project was implemented without interrupting the mill’s operations. The work included replacing the existing PLCs in the fiberline and in the existing evaporation system, as well as replacing the automation of the ETA/ETAC (water treatment plant) and causticizing section.
“This was one of the main – if not the most important – investments in recent years at Irani. We focus on the company’s sustainability, and we chose Valmet because it is a reliable company that offers technology aligned with our project,” explains Henrique Zugman, Director of Paper and Forestry at Irani.
“With the DCS, we can now track operations, identify the cause of potential problems, and solve them quickly,” says João Santos, Maintenance Manager at Irani.
“The reason for the success of our project was the exemplary synergy between the Valmet and Irani teams during implementation. The result was remarkable, with the delivery not only meeting our customer’s expectations but also achieving the vital milestone of zero accidents,” reports Sérgio Bandeira Junior, Operations Director of Automations Systems in South America at Valmet.
Valmet DNA selected for ease of use
The Valmet DNA Automation System was chosen for its intuitive and interactive interface, facilitating the transition of operators to the new system. It provides an easy-to-understand interface for controls, analysis, configuration, and maintenance. The excellent usability simplifies operations and allows users to manage larger process areas more easily. The Remote Field cabinets also provide operational flexibility and substantial cost savings with field cabling.
The DCS lets us track operations, identify the cause of potential problems, and solve them quickly.
“With the DCS, we can now track operations, identify the cause of potential problems, and solve them quickly. This means the plant has greater availability and productivity. In addition to being a controller, the system stores data. Today, we have more than 12,000 tags being inspected and recorded simultaneously. The system has provided us with better operation, coordination, and management of activities,” adds João Santos, Maintenance Manager at Irani.
The project exceeded expectations for the DCS implementation.
Easy access to historical data
One of the new system’s highlights is Tracer, Valmet’s integrated trend history analyzing tool. This tool allows the acquisition and provision of process data, which is presented to operators using interactive graphs and KPIs. Today, around 100 percent of the historical data is stored in the Irani system. The data can be transformed into detailed production reports and management dashboards, facilitating the centralization of information and ensuring its correct distribution to users.
“Another important factor with this tool is that it is more than just a supervisory system; it has a native historian that offers several resources. We don’t need to purchase additional software, generate an interface, or hire an engineering team to develop the historian. The functionality is integrated into the tool itself, with complete dashboards and reports. We were able to unify everything into a single system that generates results in the short, medium, and long term,” says Hernandez Camargo, Irani’s Automation Coordinator at the Vargem Bonita mill.
Comprehensive distributed control system delivery
Valmet provided a comprehensive delivery, which included several stages in a DCS implementation project. The scope included the detailing and design of the system, the engineering development of the application, the manufacture of the I/O cabinets, the factory acceptance tests of the entire application and cabinets, and the installation of the system at mill. The system and plant were then commissioned and started up. Currently, all process areas are integrated into a single platform, facilitating user access to data and encouraging collaboration. The Valmet DNA Automation System is a future-proof solution, with the ability to easily include extensions for Industrial Internet applications.
The Irani paper mill in Vargem Bonita, Brazil.
Digital transformation journey
The implementation of the new DCS is one of the steps in the company’s strategy to boost its business through digital transformation. “We are working on digitalizing the mill, including implementing advanced process controls (APC), to make advances in applications related to Industry 4.0. We are also assessing how to use artificial intelligence components to increase the autonomy and reliability of the factory and make it even more competitive,” concludes Zugman.
Text Livia Bianco
PHOTOS Angelo Felice